Die Kesselspeisepumpe ist eine andere Bezeichung für die Speisepumpe (siehe Reaktorpumpe) und eine mehrstufige Radialpumpe. (siehe auch Mehrstufige Pumpe)
Ihre Aufgabe besteht darin, einem Dampferzeuger wie einem Kessel oder Kernreaktor die der abgegebenen Dampfmenge entsprechende Speisewassermenge wieder zuzuführen. Heute kommen hierfür nur noch Kreiselpumpen zum Einsatz. Die Ausführung von Kesselspeisepumpen in Bezug auf Leistungsbedarf, Werkstoff, Pumpenbauart und Antrieb ist wesentlich durch die Entwicklung der Kraftwerkstechnik bestimmt worden. So geht der Trend bei konventionellen Kraftwerken zu immer größeren Blockeinheiten (> 1000 MW, Stand 2011). Dies führt bei den Kesselspeisepumpen zu Antriebsleistungen von 30-50 MW.
Der durchschnittliche Druck im Austrittsquerschnitt (Speisepumpenenddruck) lag bis zum Jahr 1950 bei 200 bar. Bereits im Jahr 1955 waren diese Enddrücke bis auf 400 bar gestiegen. Die Masseströme lagen bis 1950 im Bereich von 350 t/h und sind heute bis 3.200 t/h (in Ausnahmen bis 4.000 t/h) angestiegen. Die Kesselspeisepumpen arbeiten bei Temperaturen von 160 bis 210 ºC und in Ausnahmen bei noch höheren Temperaturen des Fördermediums.
Für Kernkraftwerke mit 1.600 MW Leistung werden die Speisepumpen für Masseströme bis zu 4.000 t/h und Speisepumpenenddrücke von 70 bis 100 bar ausgeführt.
Kesselspeisepumpen wurden bis etwa 1950 aus unlegierten Stählen und danach aus Stählen mit 13-14 % Chromgehalt hergestellt. Die Werkstoffumstellung war aufgrund einer veränderten Speisewasserchemie notwendig geworden. Durch die Entwicklung hochfester, korrosions- und erosionsfester martensitischer Chromstähle mit guten Notlaufeigenschaften und der stetigen Weiterentwicklung aller Pumpenkomponenten (Lagerung, Wellendichtung, Pumpenhydraulik etc.) entstand die heutige Kesselspeisepumpe mit möglichen Drehzahlen zwischen 4.500 und 6.000 min-1. Die Masseströme der Kesselspeisepumpe stiegen mit den schnell wachsenden Blockleistungen an, sodass Volllastspeisepumpen für konventionelle 800 bis 1.100-MW-Blöcke heute vier- bis sechsstufig mit Stufendrücken bis ca. 80 bar ausgeführt werden, während die für 1.600-MW-Kernkraftwerke einstufig ausgeführt werden.
Antrieb
Bei konventionellen Anlagen über 500 MW wird der Antrieb der Volllastspeisepumpe zunehmend mit einer Dampfturbine realisiert. Meist werden Kondensationsturbinen im Nenndrehzahlbereich von 5.000 bis 6.000 min-1 verwendet. Elektromotoren dienen meist zum Antrieb von Teillastspeisepumpen sowohl bei fossilbefeuerten als auch bei nuklearen Kraftwerken. Die Drehzahlverstellung erfolgt bei elektromotorgetriebenen Speisepumpen entweder mittels Strömungskupplung (z. B. Turbo-Regelgetriebe) oder durch Regelung auf elektrischer Seite mittels Thyristoren (bis ca. 18 MW Antriebsleistung, Stand 2011). Der Aufbau des Kesselspeisepumpenaggregates ist in vier Varianten heute gängig.
siehe Abb. 1 Kesselspeisepumpe
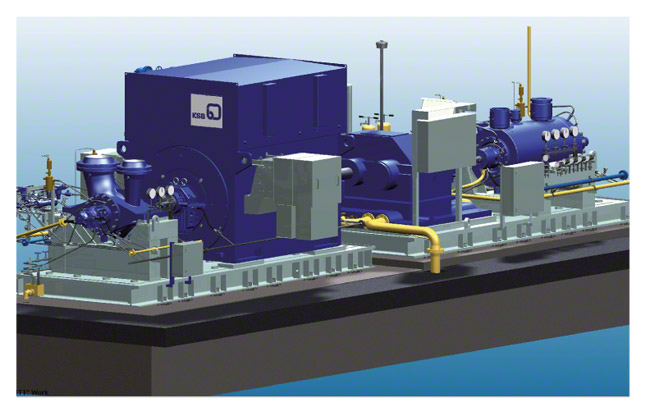
Die langsam laufende Vorpumpe wird meist von einem freien Wellenende der Turbine über ein Untersetzungsgetriebe oder direkt vom freien Ende des Elektromotors angetrieben.
siehe Abb. 2 Kesselspeisepumpe
-data.jpg)
Die ein- oder zweiströmige Vorpumpe hat hier die Aufgabe, den NPSHR-Wert der Anlage für die nachgeschaltete hochtourige Kesselspeisepumpe zu erzeugen. siehe Abb. 3 Kesselspeisepumpe
-data.jpg)
Bauart
Ausgeführt werden Kesselspeisepumpen für konventionelle Kraftwerke als:
-data.jpg)
-data.jpg)
Beide Bauarten unterscheiden sich nur durch die Ausführung der drucktragenden Hülle, wodurch Differenzen in den Herstellkosten und der Montagefreundlichkeit entstehen. Keine Unterschiede zeigen sich jedoch hinsichtlich der Betriebssicherheit und der Robustheit in abnormen Betriebsbedingungen. Die Abmessungen der rotierenden Teile und der strömungsführenden Kanäle können gleich ausgeführt werden.
Zwei Gesichtspunkte für den Einsatz einer Glieder- oder Topfgehäusepumpe
- Die Material- und Herstellungskosten sind bei Topfgehäusepumpen im Vergleich zur Gliederpumpe umso größer, je kleiner der Massestrom und je höher der Druck ist.
- Die Topfgehäusepumpe bietet gegenüber der Gliederpumpe einige Vorteile bei der Reparatur in der Anlage. So kann im Falle eines Läuferaustausches das Topfgehäuse (siehe Pumpengehäuse) in dem Rohrleitungssystem installiert bleiben. Dies ist für die Verfügbarkeit eines Kraftwerkblockes relevant, wenn keine volle Pumpenreserve vorhanden oder eine Pumpe nur mit erhöhtem Aufwand austauschbar ist.
Für Kernkraftwerke sind Speisepumpen in einstufiger Bauart mit zweiströmigem Laufrad (siehe mehrströmige Pumpe) und Doppelspiralgehäuse üblich. siehe Abb. 6 Kesselspeisepumpe
-data.jpg)
Die gegossenen druckbelasteten Teile des Gehäuses werden immer häufiger durch Schmiedeteile ersetzt. Eine derartige Speisepumpe ist bspw. für einen Förderstrom von etwa 4.200 m3/h und eine Förderhöhe von etwa 700 m bei einer Drehzahl von rund 5.300 min-1 ausgelegt. siehe Abb. 5 Kesselspeisepumpe
Die Förderhöhen der Reaktor-Speisepumpen liegen für Siedewasserreaktoren im Bereich von 800 m, für Druckwasserreaktoren um 600 m. Die Förderströme entsprechen jedoch ca. dem doppelten Wert einer vergleichbaren Kesselspeisepumpe eines fossilbeheizten Kraftwerkes.
Gehäuse
Die Gehäuse der Kesselspeisepumpen sind unter zwei Gesichtspunkten zu betrachten: Einerseits muss eine den Druckbeanspruchungen gerechte und andererseits den unterschiedlichen zeitlichen Temperaturverhältnissen angepasste Wanddicke angestrebt werden. Diesen beiden Kriterien wird ein hochfester ferritischer Gehäusewerkstoff gerecht, der die Wanddicken so minimiert, dass aufgrund von Temperaturänderungen keine Überbeanspruchung und eine ausreichende Sicherheit gegenüber dem Innendruck gewährleistet wird.
Topfgehäuse
- Die Topf- oder Mantelgehäuse werden meist aus un- oder niedrig legiertem zähen Schmiedestahl hergestellt und sämtliche von strömendem Speisewasser benetzten Funktionsflächen mit korrosions- und erosionsfestem Werkstoff durch Auftragsschweißung beschichtet.
- Beim Einschweißen der Pumpe in die Rohrleitung muss ein Zwischenstück vorgesehen werden, wenn die zu verbindenden Stutzenmaterialien nicht aus derselben Werkstoffgruppe stammen.
- Der druckseitige und den Enddruck abdichtende Deckel des Mantelgehäuses wird mit großen Stiftschrauben drehmomentfrei verspannt. Die Dichtaufgabe übernimmt ein Profildichtring, der ohne äußere Kräfte nur durch den anliegenden Druck (bis zu mehreren 100 bar) beaufschlagt ist. siehe Abb. 7 Kesselspeisepumpe
-data.jpg)
Gliederpumpen
- Die Gehäuse von Gliederpumpen werden bevorzugt aus geschmiedetem Chrom- oder Kohlenstoffstahl mit austenitischer (Mischkristalle des Eisens) Plattierung hergestellt.
- Die Dichtung zwischen den einzelnen Stufengehäusen (siehe Stufe) erfolgt rein metallisch mittels Zugankern zum Verspannen der Stufengehäuse, sowie um Saug- und Druckgehäuse (siehe Pumpengehäuse).
- Temperaturschocks wirken sich aufgrund der unterschiedlichen, temperaturbedingten Dehnungen hauptsächlich in Form von zusätzlichen Belastungen an den Zugankern und Dichtflächen der Stufengehäuse aus.
Die beiden Pumpenbauformen Topfgehäuse- und Gliederpumpe verbindet die Eigenschaft, dass bei Temperaturschockbelastung die thermisch induzierte Spannung mit zunehmender Wandstärke zunimmt und sich vermindernd auf die Lebensdauer auswirkt. Der häufige Wunsch nach Einspritzwasser, das im Druckniveau zwischen Zulauf- und Enddruck liegt, ist durch Anzapfen einer Stufe sowohl bei der Glieder- als auch der Topfgehäusepumpe zu realisieren.
Stufenanzapfung
- bei Kesselspeisepumpen Bei der Gliederpumpe kann ein Teilstrom mit Zwischendruck in einfacher Weise durch ein Stufengehäuse mit Anzapfstutzen abgeleitet werden. siehe Abb. 5 Gliederpumpe
- Um bei der Topfgehäusepumpe mit einer Anzapfung einen Teilstrom mit gewünschtem Zwischendruck direkt nach außen abzuleiten, wird der Innenraum in drei Druckbereiche aufgeteilt. siehe Abb. 4 Topfgehäusepumpe
Die Dichtfunktion wird von einem Profildichtring zwischen End- und Anzapfdruck sowie metallisch dichtend zwischen Anzapf- und Zulaufdruck erfüllt. siehe Abb. 7 Kesselspeisepumpe
Dabei ermöglicht besonders der Profildichtring ein hohes Maß an Relativbewegung der Dichtfläche wie es bei Temperaturschocks erforderlich ist.
Läuferausführung
Die Pumpenwelle hat bei den Kesselspeisepumpen bei einem möglichst kleinen Lagerabstand und relativ großem Wellendurchmesser mit meist aufgeschrumpften Laufrädern (im Hochleistungsbereich) eine geringe statische Durchbiegung. Sie ist zumeist unempfindlich gegen Schwingungen und gewährleistet so im Normalbetrieb einen radial berührungsfreien, ruhigen Lauf (siehe Laufruhe). Die auf der Laufradrückseite verdickte Nabe und die Gestaltung der Laufradeintrittsgeometrie auf einem möglichst kleinen Durchmesser verkleinert die in der Entlastungseinrichtung aufzunehmenden Restaxialschubkräfte (siehe Axialschub). Im Vergleich zum Kesselspeisepumpenläufer sind einstufige Reaktorspeisepumpenläufer noch steifer und deren statische Durchbiegung liegt unterhalb von mehrstufigen Kesselspeisepumpenläufern.
Axialschubausgleich
Bei Kesselspeisepumpen für konventionelle Kraftwerke mit einer bestimmten Anordnung der Laufräder entsteht ein Axialschub an den Laufrädern. siehe Abb. 10 bis 12 Axialschub
Die Größe dieses Axialschubes ist von der Lage des Betriebspunktes, der Drehzahl und vom verschleißabhängigen Zustand der Innenspiele (siehe Spaltdichtung) abhängig. Zusätzliche Störkräfte entstehen bei anormalen Betriebszuständen wie bspw. bei Kavitation.
Der axiale Kräfteausgleich am Pumpenläufer erfolgt bei einer größeren Kesselspeisepumpe durch eine vom Fördermedium durchströmte hydraulische Entlastungseinrichtung häufig in Verbindung mit einem ölgeschmierten Axiallager (siehe Gleitlager). Diese Entlastungseinrichtung gleicht bereits über 90 % des Axialschubes aus, weshalb das Axiallager kleiner dimensioniert werden kann. Sie besteht aus einer Entlastungsscheibe mit Gegenscheibe, oder einem Kolben bzw. Doppelkolben mit den zugehörigen Drosselbuchsen.
Die Axialkräfte von Reaktorspeisepumpen mit zweiströmigem Laufrad (siehe mehrströmige Pumpe) sind hydraulisch ausgeglichen und Restschübe werden durch ein ölgeschmiertes Axiallager aufgenommen. siehe Abb. 6 Kesselspeisepumpe
Radialkräfteausgleich am Pumpenläufer
Die radialen Kräfte entstehen entweder durch das Gewicht des Läufers, durch mechanische Unwucht oder den hydraulischen Radialschub. Ein Kräfteausgleich erfolgt durch zwei ölgeschmierte Radiallager sowie axial durchflossene Drosselspalten. Letztere befinden sich auf der Laufradeintrittsseite am Laufradhals und bei mehrstufigen Kesselspeisepumpen von konventionellen Kraftwerken auf der Druckseite des Laufrades (Stufenbuchse), sowie am Entlastungskolben. In diesen Spalten entsteht bei exzentrischer Läuferlage eine zentrierende Rückstellkraft, die von der Druckdifferenz und der Spaltgeometrie hauptsächlich abhängig ist (LOMAKIN-Effekt). Der LOMAKIN-Effekt ist stark gemindert, wenn in anormalen Betriebszuständen das Speisewasser in der Spaltströmung nicht aus der reinen flüssigen Phase (siehe Kavitation) besteht.
Die tragende Wirkung der Drosselspalte kann erheblich mehr zur Wellensteifigkeit beitragen als die reine mechanische Steifigkeit. Das System wird so abgestimmt, dass die kritische Drehzahl des Läufers stets in genügend großem Abstand von der Betriebsdrehzahl bleibt und hydraulische Erregerkräfte (besonders im Teillastbetrieb) zusätzlich aufgenommen werden können.
Ein zusätzliches Leitrad oder eine Doppelspirale kann den Radialschub vermindern.
siehe Abb. 6 Spiralgehäusepumpe
Wellendichtung
Als Wellendichtungen werden bei den Kesselspeisepumpen die Gleitringdichtung, Schwimmringdichtung, Labyrinthdichtung und mittlerweile eher selten die Stopfbuchspackung verwendet (siehe auch Wellendichtung).
Anwärmung und Warmhaltung
In den Kesselspeisepumpen treten Belastungen bei transienten Betriebsweisen oder geringer Durchströmung der Pumpe auf, die sich mit den bereits vorhandenen überlagern. Dies verursacht zusätzliche Bauteilspannungen und Verformungen mit unterschiedlicher Konsequenz auf die Funktionalität der Maschinenkomponenten.
Heute müssen nahezu alle Kesselspeisepumpen in der Lage sein, sowohl Kalt- (Heißschockbelastungen) als auch Halbwarmstarts schadensfrei zu überstehen. Hierbei strömt schlagartig heißes Speisewasser in die kalte Pumpe. Die inneren Bauteile erwärmen sich dabei wesentlich schneller als die Druckhülle. Je nach Häufigkeit und Gradientenverlauf von Druck und Temperatur (Lastzyklen) kann dies die Lebensdauer reduzieren.
Bei besonders dickwandigen Maschinen benötigt die Wärmeausbreitung im Bauteil mehr Zeit, weshalb die inneren Spannungen höher sind.
Grundsätzlich besteht die Gefahr des Anstreifens zwischen Teilen des Rotors und Stators, da enge Spalten als innere Spaltdichtung vorhanden sind. Hiervon betroffen ist das Laufrad auf der Eintrittsseite am Laufradhals, der druckseitige Spalt zwischen Laufrad und Leitrad und Stufenbuchse sowie der Entlastungspartie mit (je nach Ausführung) mehreren Drosselspalten.
Kritische Betriebszustände wie bspw. die Dampfblasenbildung lassen sich in der Zulaufleitung nicht völlig vermeiden. Dabei treten durch den kurzzeitigen Kontakt zwischen Stator und Rotor hohe Unwuchtkräfte in diesen engen Spalten auf. Aus diesem Grund muss die Werkstoffpaarung neben der ohnehin notwendigen Korrosions- und Erosionsbeständigkeit ein besonders gutmütiges Verschleißverhalten (Notlaufeigenschaft) aufweisen. Gute Erfahrungen wurden mit profilierten Chromstählen und besonderer Spaltgeometrie gemacht.
In Betriebssituationen sehr geringer oder keiner Durchströmung wie im Drehwerkbetrieb einer turbinenbetriebenen Kesselspeisepumpe kommt es zur Bildung von Temperaturschichten im Fördermedium, sodass sich sowohl die Rotoren als auch mit leichter Verzögerung die sich nicht drehenden Bauteile verformen können. Wird dabei das Spiel in den Drosselspalten aufgebraucht, erfährt der Rotor ein wesentlich höheres Reibmoment, wodurch es zu einer Überlastung des Drehwerkantriebs und damit zum Pumpenstillstand kommen kann. Da in diesem Fall dann auch kein Temperaturausgleich am Rotor mehr stattfindet, wird die Rotorverkrümmung noch kritischer. Dies kann zu einem mehrstündigen Aggregatsausfall führen. Meist hilft dann nur das Abkühlen der Maschine, um die Reduzierung oder Beseitigung der kritischen Wärmeschichtung und damit der Verkrümmung zu erreichen.
Um ein möglichst optimales thermisches Verhalten der Pumpe herbeizuführen, sind verschiedenste Maßnahmen anzuwenden.
Vermeidung von großen Temperaturunterschieden in und an der Pumpe
- gute thermische Trennung der kalten Bereiche (Wellendichtungsbereich) vom heiß durchströmten Bereich (Hydraulikbereich und Entlastungseinrichtung) mit Isolierkammersystem; Thermosperre zur Verhinderung von Konvektionsströmen und speziellen Thermohülsen
- Pumpe außen isolieren
- Anwärmung oder Warmhaltung durch Zwangsdurchströmung der Maschine meist über die eingedrosselte Druckschiene
- temporäre oder dauerhafte Kühlwasserunterbrechung im Gleitringdichtungsbereich (sekundärseitig)
- Begrenzung der Betriebsführungsparameter für kritische Betriebszustände (ΔT) (am Mantelgehäuse oben-unten) und/oder ΔT-Gehäuse zu Speisewassertemperatur
Abschwächung der Folgen von großen Temperaturunterschieden
- bei Standby-Betrieb Pumpe im Drehwerk drehen
- Drehwerk synchronisiert ausführen (Minimierung oder Vermeidung echter Stillstandzeiten)
- Wasser aus kritischen thermischen Bereichen abführen
Verwendung thermisch gutmütiger Wellendichtungen
- berührungsfreie Dichtung (Schwimmringdichtung)
Da Mantelgehäusepumpen (Topfgehäusepumpen) aufgrund ihrer Außenabmessungen, Wandstärken, Antriebsart (Turbine mit Drehwerk) und Betriebsweisen im Vergleich zu Gliederpumpen als kritischer gelten, finden die beschriebenen Maßnahmen hier vermehrt Anwendung. Zur Absicherung der Verfügbarkeit des Pumpenaggregats werden diese Maßnahmen falls möglich automatisiert ausgeführt.
Mindestförderstromventil
Ein Mindestförderstromventil (Freilaufrückschlagventil) sichert einen Mindestförderstrom und verhindert Schäden, die im Schwachlastbetrieb (siehe Teillastbetrieb) infolge von unzulässiger Temperaturerhöhung mit Verdampfung des Pumpeninhaltes sowie durch Teillastkavitation auftreten können.