Propeller pump
A common feature of a ship's propeller, a propeller-type mixer and a propeller pump is the axial flow impeller (see Axial flow pump and Propeller).
Propellers can be designed with fixed-pitch blades (fixed-pitch propeller), blades whose pitch can only be adjusted with the propeller dismantled (adjustable-pitch propeller) or blades whose pitch can be adjusted during operation (variable-pitch propeller). For this reason a pump with adjustable vanes in a mixed flow impeller is also referred to as a propeller pump.
Of all centrifugal pumps, propeller pumps have the highest specific speeds (ns > 110 rpm) but are used most commonly for ns > 160 rpm. The higher the specific speed, the smaller the number of impeller blades, the less pronounced the profile convexity and the smaller the hub-to-tip ratio.
Propeller pumps are suitable for large flow rates and low heads (up to approximately 15 m in a stage with an axial flow propeller and 20 m in a stage with a mixed flow impeller).
Their H/Q curve is steep compared to that of other centrifugal pumps; the cut-off point marks the operating behaviour of this pump type. See Figs. 3, 4 Characteristic curves selection chart and Figs. 1, 4 Characteristic curve
The power input curve (see Characteristic curve) reaches its maximum at zero flow, which is why propeller pumps are started up against an open discharge-side gate valve to prevent overloading of the drive (during the start-up process). The typical characteristic curve (with a "saddle" and "cut-off point" and with the power input increasing as flow rate decreases) makes considering the otherwise uneconomical bypass adjustment worthwhile as a control option: Opening of a bypass line reduces the power input and head while increasing the effective flow rate.
The impeller blade pitch and with that the volume flow rate and "cut-off point" can be adjusted during operation using mechanical, electric or hydraulic adjustment gear (see Impeller blade pitch control). This type of control is very commonly used for propeller pumps. Blade pitch adjustment with the propeller dismantled can be used for altering the head without having to fit any new components or re-machine fitted components. Variable-pitch propeller pumps are started up at minimum pitch angles, i.e. minimum power input.
Axial flow propeller pumps (see Fig. 1 Pump casing) are commonly designed as tubular casing pumps mixed flow propeller pumps can either be tubular casing pumps or volute casing pumps (with a concrete casing for large pump sizes).
In tubular casing pumps the pump shaft is usually supported by water-lubricated shaft guide bearings (see Plain bearing) in the column pipe. The axial thrust is absorbed by a sturdy axial bearing (see Plain bearing and Rolling element bearing) installed above the gland packing. See Fig. 1 Propeller pump
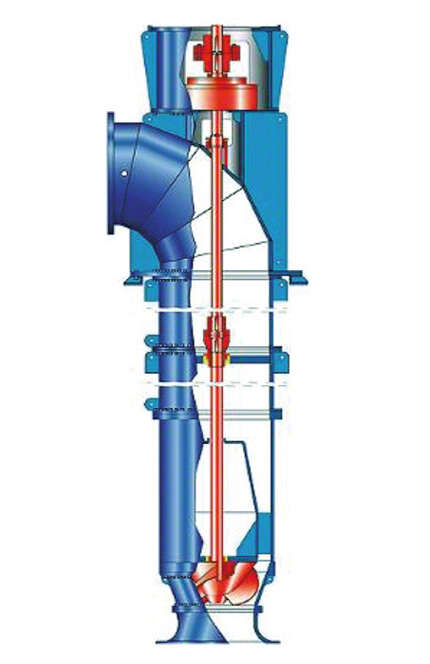
Fig. 1 Propeller pump: Tubular casing pump with mixed flow propeller
Since the flow in axial flow impellers is very sensitive to disturbances in the approach flow, particular attention must be paid to the design and implementation of the intake chambers, bellmouths or intake elbows (see Inlet conditions).
Propeller pumps can be several metres in diameter.
Propeller pumps are usually designed with a single stage; for higher heads axial multistage propeller pumps are employed in individual cases, making use of impeller blade pitch control. Compared to single-stage axial flow pumps, the costs are considerably higher for multistage variable pitch propeller pumps or propeller pumps with a rotating assembly which can be pulled out (see Pump in pull-out design).
If higher heads are required, the more common alternative is to adopt a propeller pump with a mixed flow impeller (see Propeller) or a mixed flow pump. In this case, the impeller vanes (blades) of the propeller pump face in the direction opposing the main flow; their adjustable axes are set to an angle of 25º to 45º against the radial direction. A propeller pump with mixed flow propeller blades combines the advantages of the high heads of mixed flow impellers with the good control capabilities of variable pitch propellers.
Propeller pumps are employed as land reclamation pumps (see Pumps for use in low-lift pumping stations) (drainage and irrigation), as cooling water pumps (power stations, on board vessels), as circulating pumps (boiling water reactor, heating system), as universal elbow casing pumps (in the chemical and food processing industries) as well as for generating thrust with a propeller in a transverse thruster. See Fig. 2 Propeller pump
-data.jpg?ci_url_encoded=1&force_format=webp&q=60)
Fig. 2 Propeller pump: Elbow casing pump (also without diffuser for both flow directions), with adjustable blades