Rolling element bearing
The rolling element bearing is used to support shafts and consists of the bearing races or discs and the rolling elements which can be spherical, cylindrical, tapered or barrel-shaped. See Fig. 1 Rolling element bearing
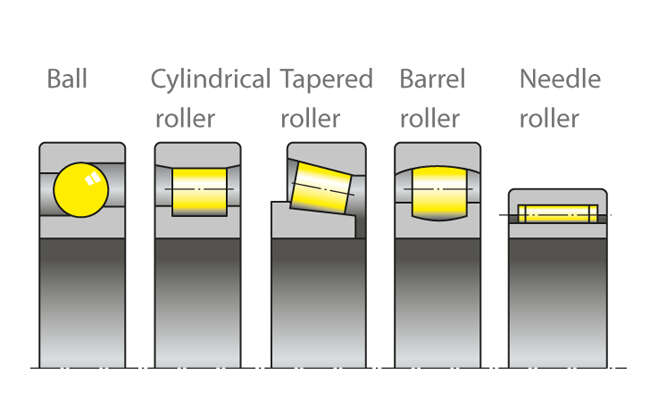
Fig. 1 Rolling element bearing: Rolling element types
In addition, they are frequently equipped with a cage which prevents contact between adjoining rolling elements. See Fig. 2 Rolling element bearing
-data.jpg?ci_url_encoded=1&force_format=webp&q=60)
Fig. 2 Rolling element bearing: Rolling element cages
Depending on the direction of force, a distinction is made between transverse (radial) bearings, axial (thrust) bearings and designs such as radial deep groove ball bearings which can handle both radial and axial forces. See Fig. 3 Rolling element bearing
-data.jpg?ci_url_encoded=1&force_format=webp&q=60)
Fig. 3 Rolling element bearing: Rolling element bearings for different load directions
Fig. 4 Rolling element bearing shows a typical shaft bearing arrangement for a low-pressure pump with cylindrical roller and angular contact ball bearings.
In radial bearings, the rolling elements run between races or rings (ring bearing), and in axial or thrust bearings they run between discs (disc bearing).
-data.jpg?ci_url_encoded=1&force_format=webp&q=60)
Fig. 4 Rolling element bearing: Cylindrical roller bearing and angular contact ball bearing in a centrifugal pump
Advantages of rolling element bearings over plain bearings
- Friction coefficient is approx. 25 to 50 % lower
- Thanks to narrower clearance gap, they run more precisely
- Require less space
- Straightforward maintenance
- Straightforward lubricant requirements
- Replaceability assured by extensive standardisation
Disadvantages of rolling element bearings over plain bearings
- Sensitive to shock loads
- More noise during operation
- Generally more expensive than comparable plain bearings
- Wear during standstill (pitting)
The load capacity and service life of rolling element bearings are standardised (DIN 622). A distinction is made between the dynamic and static load capacity. The calculation is preferably carried out in accordance with DIN 622 or in accordance with the rolling element bearing’s manufacturer.
Dynamic load capacity
- (Service life) It defines the number of revolutions or operating hours which the bearing will sustain without symptoms of material fatigue on all bearing components.
Static load capacity
- The term "static load capacity" refers to the static load force that causes a permanent deformation on the rolling element at the point of contact without impairing the bearing's function.
As the rolling velocity increases, so do the centrifugal forces acting on the rolling elements. The bearing's operating temperature increases as a result of higher friction losses; this means that each standard bearing has an upper rotational speed limit. This limit speed can easily be calculated as a function of the bearing type, size, type of lubrication and load; the equations to be used are supplied by bearing manufacturers in their catalogues.
A complete separation of the contact faces by a load-bearing lubricant film does not take place due to the rolling contact motion of the rolling elements. Conventional lubrication with greases or oils of an appropriate consistency is adequate.
The bearing manufacturer usually provides lubrication recommendations which detail the influence of the bearing's operating temperature and the ageing stability of the recommended greases and oils under the prevailing operating conditions, and usually give directions regarding topping up the lubricant fill.
Grease types for rolling element bearing lubrication
- Calcium soap greases are water-repellent and need to be topped up at frequent intervals. The operating temperatures range from -20 °C to 50 °C.
- Sodium soap greases have good lubricating properties, but absorb water; they are washed away if water penetrates the bearing. The operating temperatures range from -30 °C to 110 °C.
- Lithium soap greases are water-repellent and can sustain high loads. The operating temperatures range from -30 °C to 125 °C.
- Multi-complex soap greases are water-repellent; there is no restriction as to their applications, but are more expensive. The operating temperatures range from -25 °C to 150 °C. Examples are barium-calcium or lithium-magnesium-strontium.
Choice of solid lubricants used for special applications
- Graphite is often used in conjunction with other carriers or lubricants. The operating temperatures are below 400 °C, otherwise risk of oxidation.
- Molybdenum disulphide is a commercial lubricant available in powder form or mixed with pastes, greases or oils. The friction coefficient is very low and sinks even lower with increasing load.
It can be used in powder form for temperatures from -180 °C to 450 °C.
The trend is towards for-life lubrication, meaning that the initial lubricant fill lasts for the bearing's entire service life.