Country, region and language selection
Europe
- Austria
- Belarus
- Belgium
- Croatia
- Czech Republic
- Denmark
- Estonia
- Finland
- France
- Germany
- Great Britain
- Hungary
- Italy
- Latvia
- Lithuania
- Netherlands
- Norway
- Poland
- Portugal
- Romania
- Russia
- Serbia
- Slovakia
- Slovenia
- Spain
- Sweden
- Switzerland
- Turkey
- Ukraine
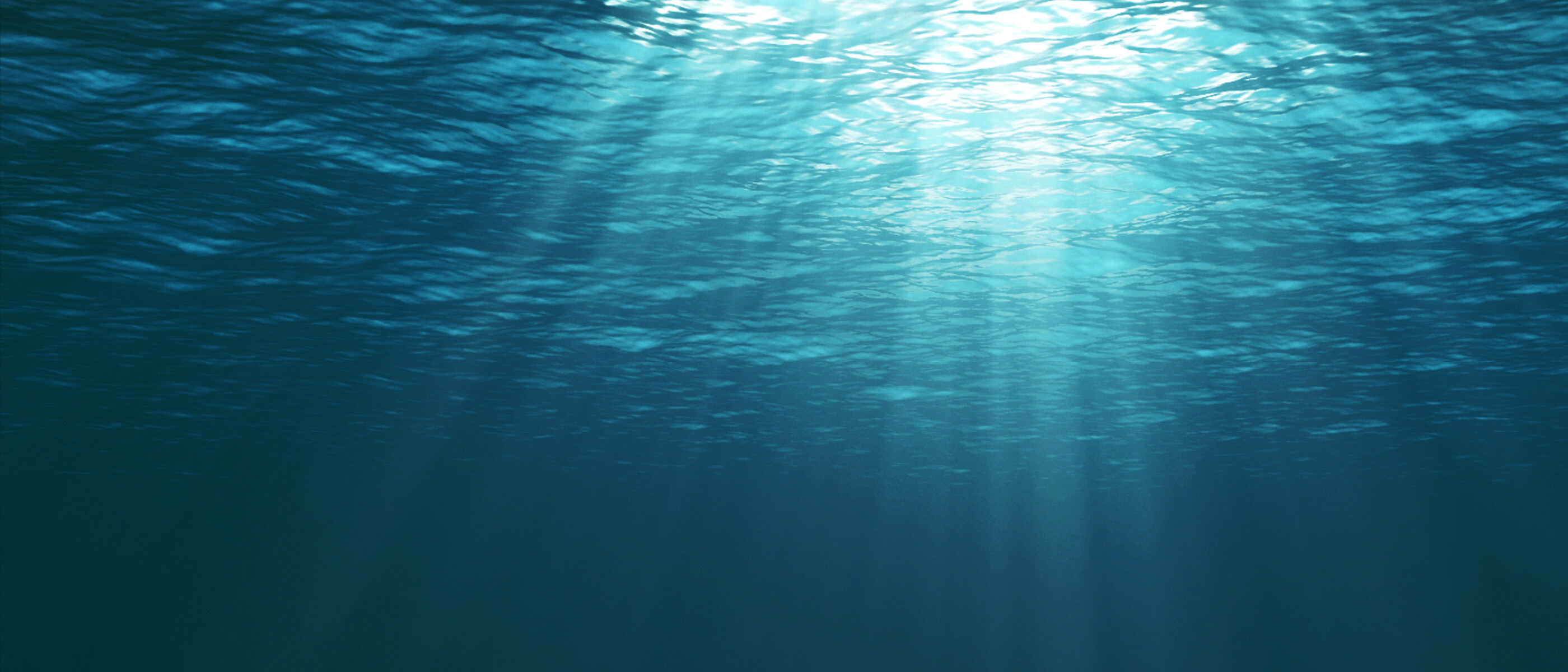
ANNUAL REPORT 2023 PUBLISHED
Investing in KSB ─ Key data at a glance
Press
More news from the company
- High-tech containment shroud for mag-drive pumps
- KSB closes the 2023 financial year with record performance
- Valves for green wind power rotors
- Additive manufacturing DNV AMC 3 certified
- KSB share in Prime Standard
- Range of high-performance water pumps expanded
- Preliminary figures for 2023
- New high-efficiency mixers
- New break tank package booster sets for fire fighting meet DIN 14462: 2023-07
- KSB very satisfied with performance in the first three quarters