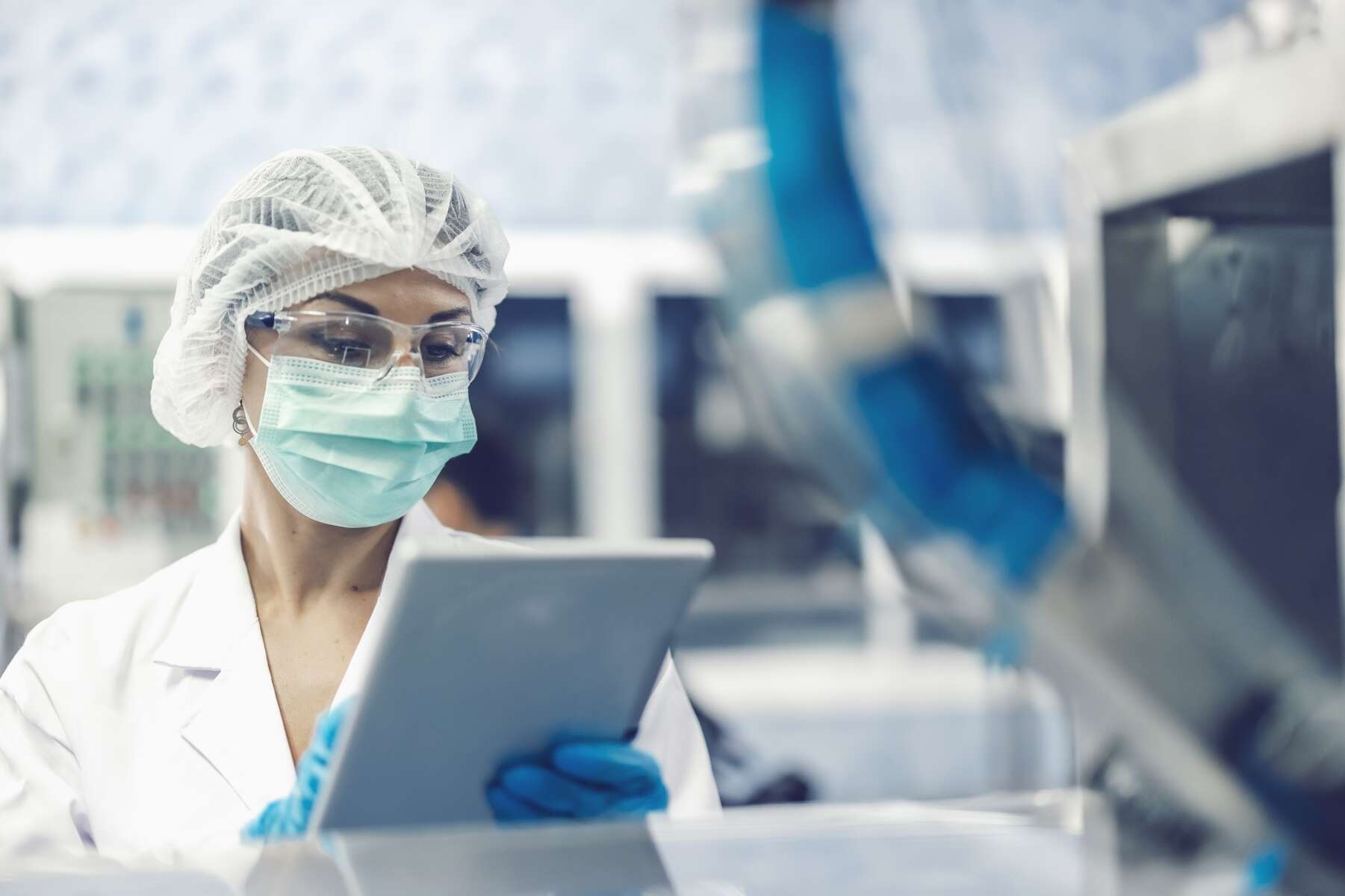
Valves for the pharmaceutical industry: How valves ensure the quality of medication
Valves for the pharmaceutical industry: How valves ensure the quality of medication
The average age of the world’s population is rising, and so is the need for new medication and progressive production processes in the pharmaceutical industry. Diaphragm valves play a key role in securing efficient and contamination-free production.
Biologics offer new opportunities
An especially dynamic field of developing new medication is that of biologics. These medicines are produced using living cells into which human genes have been introduced. They enable highly precise and often very effective treatment approaches that could not be achieved with conventional medicines. For example, gaining insulin from bacteria or yeast cells rather than from the pancreas of animals has made its production more reliable and efficient. Another example is that of monoclonal antibodies that are used to treat cancer and autoimmune diseases, e.g. Trastuzumab for breast cancer and Adalimumab for rheumatoid arthritis.
As biologics are often large, complex molecules such as proteins or antibodies, produced in living cells, their production differs considerably from the chemical synthesis of conventional medication. Biologics production is a complex process that requires precise control and specialised technologies.
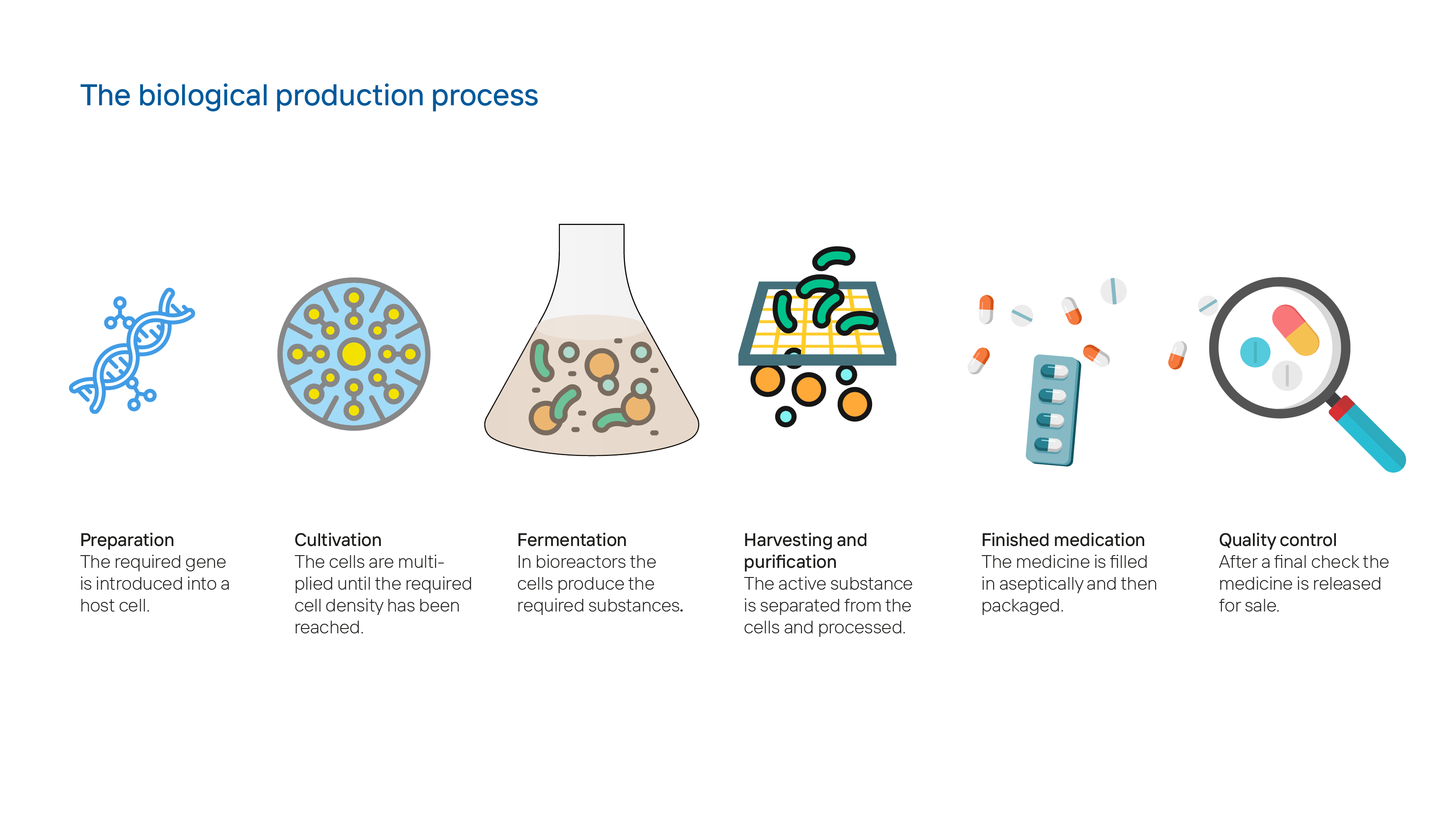
The first step is to identify and isolate the gene for the required protein or antibody. This gene is then integrated in a human or animal host cell, a bacterium or a yeast cell. This is what will produce the required protein. About 80 percent of all biologics are made using CHO cells (Chinese hamster ovary cells), all of which are traced back to cells from the ovaries of a single Chinese hamster that were extracted at the University of Colorado in 1957.
During cultivation, also called the upstream process, the altered cells are cultivated in bioreactors, where they produce the required protein. Bioreactors may comprise several thousand litres and are designed allowing for precise control of factors such as temperature, pH, oxygen feed and nutrient concentration. After the cultivation, the cells and the culture medium are harvested.
This is followed by the downstream process, where the culture medium with the cells is purified. Filtration, centrifugation or chromatography remove cell debris, by-products and other contamination. Finally, the protein is processed to achieve a stable formulation. It is then filled into small bottles, syringes or other administration types under sterile conditions. In all these processes, valves such as KSB’s SISTO-C diaphragm valve are key in providing accurate control.
Complex processes require precise control
The production of biologics is a complex process that places high demands on valves. As modern bioreactors are usually fully automated, they require valves than can be integrated in a process control system for all production steps to be precisely monitored and controlled. The content of oxygen, CO₂ and nutrients in the bioreactors has to be controlled accurately as any fluctuations could impair the growth of cells and the quality of medicines produced.
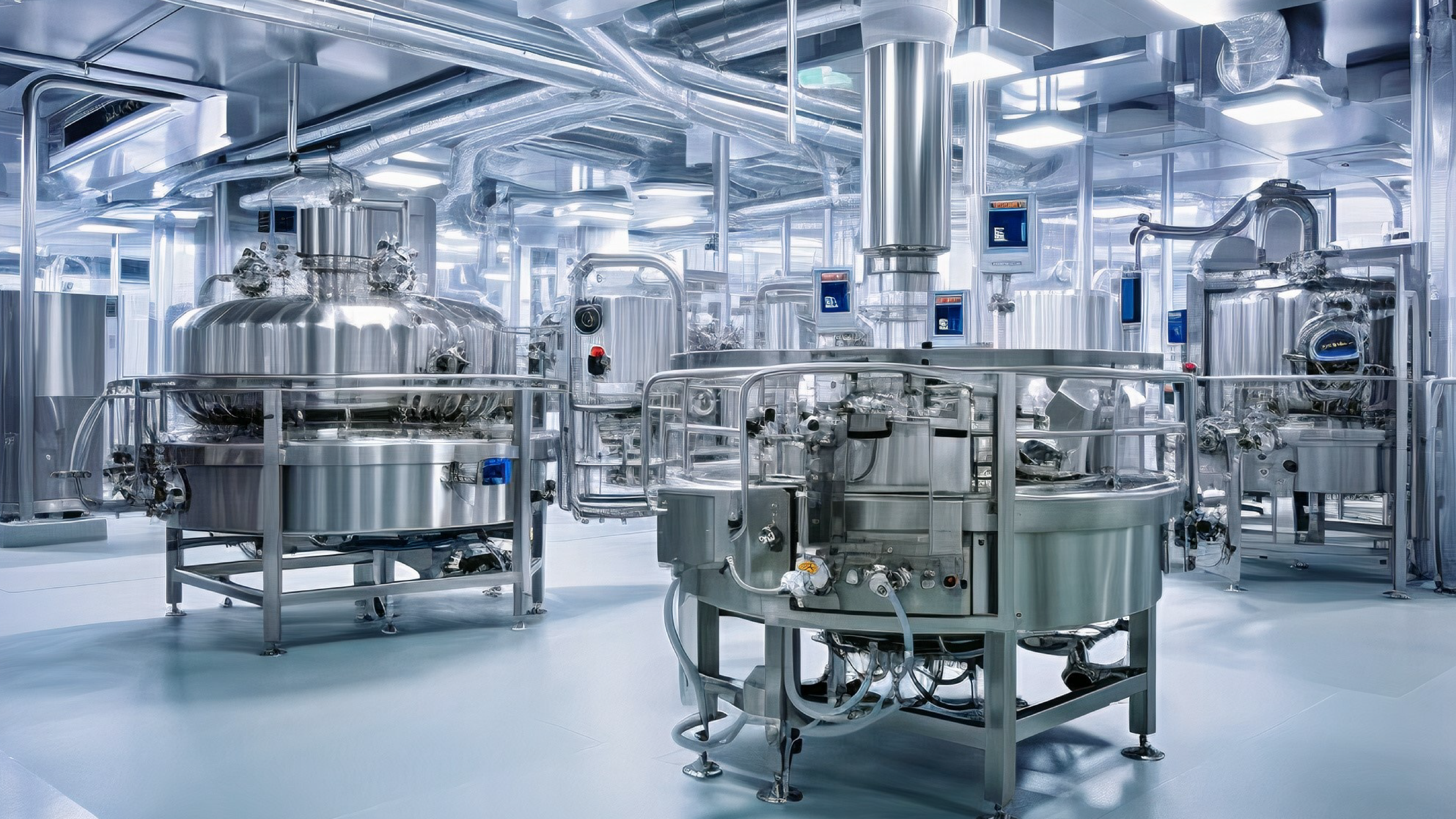
View of an industrial bioreactor
Hygiene is particularly important for pharmaceutical valves because contamination with bacteria, fungi or viruses can lead to costly production failures. Right from the development phase, attention has to be paid to cleanability, self-draining ability, zero dead volume, and suitable materials. During production, high quality standards have to be met to ensure the required surface quality. Also, the valves should be suitable for clean-in-place (CIP) and sterilise-in-place (SIP) processes, enabling them to be cleaned and sterilised without removing them from the system. To meet these requirements, pharmaceutical systems are subject to stringent validation processes, for example to the Good Manufacturing Practices of the EU or the Guidelines of the International Society for Pharmaceutical Engineering (ISPE).