Country, region and language selection
Europe
- Austria
- Belarus
- Belgium
- Croatia
- Czech Republic
- Denmark
- Estonia
- Finland
- France
- Germany
- Great Britain
- Hungary
- Italy
- Latvia
- Lithuania
- Netherlands
- Norway
- Poland
- Portugal
- Romania
- Russia
- Serbia
- Slovakia
- Slovenia
- Spain
- Sweden
- Switzerland
- Turkey
- Ukraine
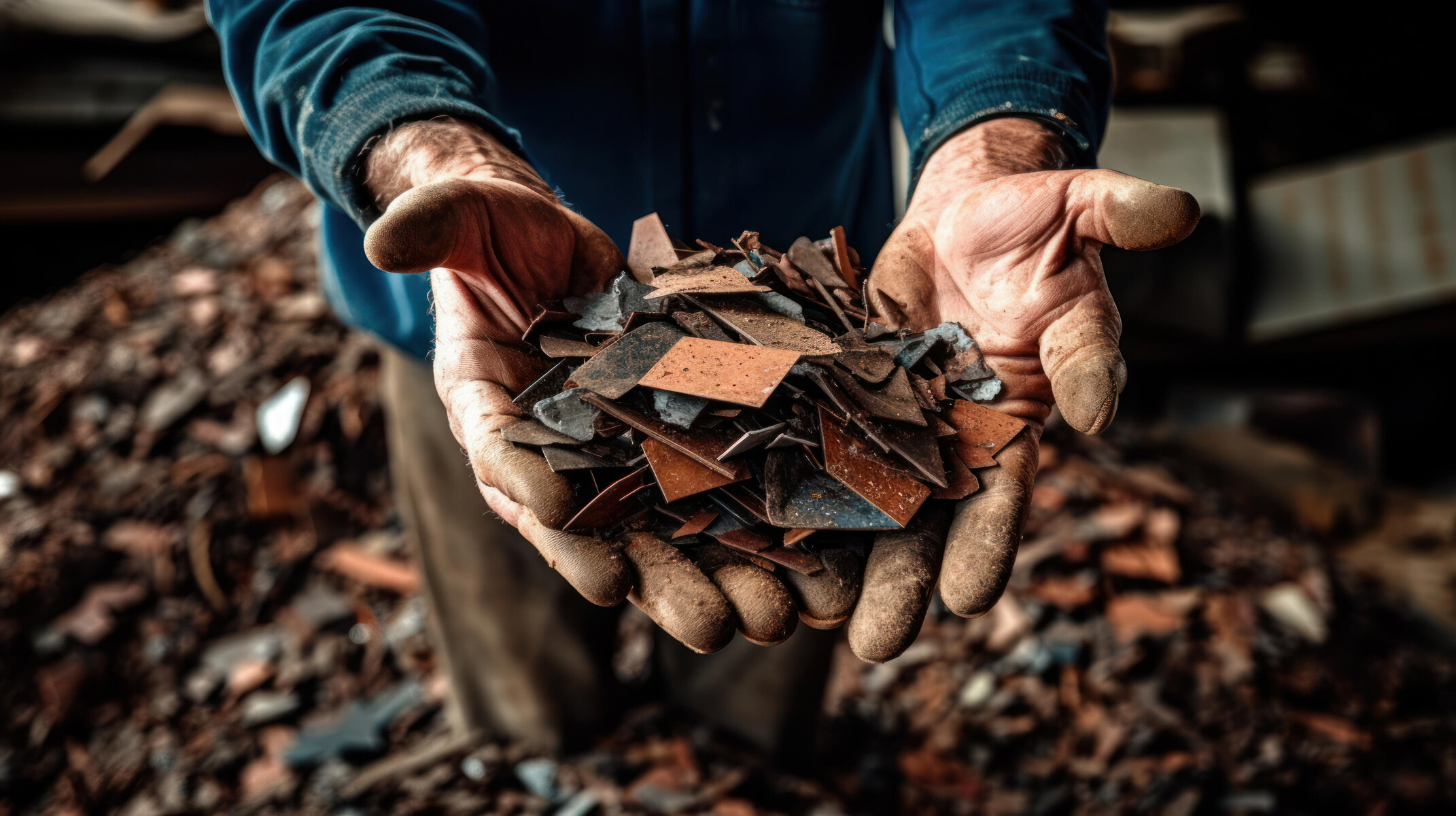
How can we realise a circular economy?
Maximising value, minimising waste
Produce, use, dispose: Not only climate change and the growing rubbish dumps around the world increasingly question this linear economic model. High energy prices, fragile delivery chains and geopolitical uncertainties also underline the necessity for a circular economy. At KSB, the principles of a circular economy are already being lived out.
By joining the UN Global Compact in 2010, KSB committed itself to sustainable business practices. For KSB, introducing a circular economy was not only driven by moral motives but also by economic ones. "This is how we can further increase our customer satisfaction," explains Daniel Gontermann, Head of Technical Product Management at KSB in Frankenthal. The principles of a circular economy meet the customers' requirements, he continues. In his daily work he can feel that the transition to a circular economy is indispensable: "We are dealing with customers who want to know exactly how much recycled material is contained in our products." They, too, want and should ensure they are purchasing pumps and valves that are not only effective and durable but also minimise the ecological footprint. And there are legal obligations to be met, he adds.
Making sustainability measurable
Recycling has got a long tradition in the pump industry: As pumps and valves are largely made of metal, decommissioned units are melted, so new components can be cast. But circularity goes far beyond recycling. To be able to assess the sustainability of a product, a number of questions have to be addressed: What materials is it made of? What is the materials’ history? How long is the service life of the product? And how likely is it for its components to be re-used?
For an objective answer to the circularity of pumps and valves, KSB has introduced the Material Circularity Indicator (MCI) for selected products. This creates transparency. The MCI value was developed by the British Ellen MacArthur Foundation and serves to support companies in assessing their products regarding the principles of circularity. "The MCI is an indicator that helps me express the percentage of recycled material a product was made of and – when the product dies – how much of it can be recycled again," summarises Rainer Michalik, Head of Integrated Management Systems and Sustainability at KSB.
The value is a number between 0 and 1. A value of 1 stands for a product made completely of recycled materials and whose raw materials can later be recycled without any losses. “Our goal is to improve the MCI of five of our products by 20 percent before the end of 2024 – currently these are Calio, EtaLine Pro, Amarex N, AmaDrainer 3 and PumpDrive 3,” explains Daniel Gontermann. "The Calio heating circulator has currently got an MCI of 0.35 but we would like to achieve 0.42. The Amarex N submersible pump is already at 0.7 – that’s already a good value." KSB wants to pull all the right levers to increase its products’ MCI. "Also when procuring pre-products the percentage of recycled materials is something we take more and more into account," adds Daniel Gontermann.
Flexibility provides more sustainability
The longer pumps and valves remain in operation, the more sustainable they are. If changes are made to a customer’s plants and systems, the pumps installed may no longer be a good fit for the system. They may have to be modified or replaced.
For instance, the impeller might have to be replaced when the flow rate rises due to added systems and machinery. In the past, such mechanical alterations often proved to be uneconomical. In such cases, a completely new pump was required – which was not sustainable at all. "Nowadays, for the EtaLine Pro type series, we can make various adjustments to the pumps using a software program, Bluetooth and an app. This extends the service life of our products significantly," explains Daniel Gontermann. The pumps’ adaptability is comparable to a light whose brightness can be adjusted very precisely, just as required, by means of a dimmer. This smart option, called "tune to process", also brings another benefit: "It has also enabled us to reduce the number of pump sizes," continues Daniel Gontermann. We have lowered the number from about 40 to approximately 15, streamlining logistics and lessening the environmental impact.
3D printing prevents pump oldtimers from ending up in the dump
Frequently, pumps and valves have to be decommissioned because their spare parts are no longer available. If specific components were lacking in the past because the model was no longer being produced, the only option was to provide the customer with a quote for a new product. Additive manufacturing – colloquially referred to as 3D printing – is an option of quickly producing spare parts for models whose production has been discontinued. This can also be done for competitor models.
"Within a very short timeframe we can print a new impeller for a pump, for example, and hand it over to the customer. In emergencies, depending on the size, this can even be done within 48 hours," says Daniel Gontermann. Logically, these options have got a huge impact on the service life extension of KSB products. 3D printing is not only fast; it also saves material – another reason for further optimising this field in the future. Gontermann: "In the future, we will exclusively manufacture certain components in the pump by 3D printing because this process is markedly more effective on several levels."