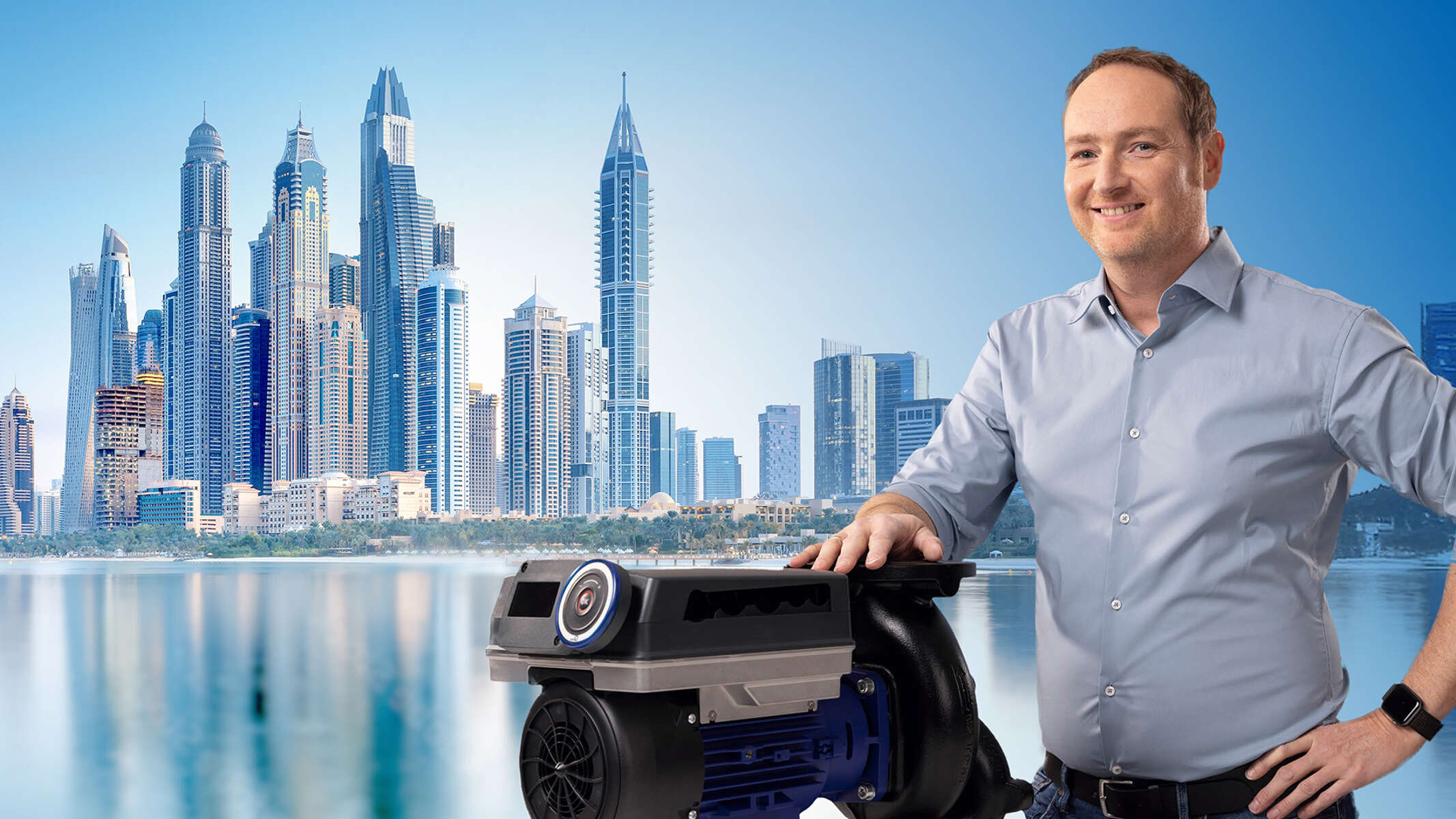
EtaLine Pro as an overall system: An interview with Steffen Horchler
What are the benefits of a pump not being assembled from individual components but consistently designed and manufactured as an overall system, right from the start? We asked the KSB expert and EtaLine Pro Product Manager, Steffen Horchler.
What are the benefits of a pump not being assembled from individual components but consistently designed and manufactured as an overall system, right from the start? We asked the KSB expert and EtaLine Pro Product Manager, Steffen Horchler.
A completely new approach in pump development
KSB Magazine: Hello Mr Horchler, you have been employed with KSB since 2002 and are currently working as Product Manager for the newly developed EtaLine Pro in-line pump. Could you please introduce your new "baby" to us?
S.H.: With pleasure. The new EtaLine Pro is a completely novel in-line pump. We initially developed it especially for building services applications.
KSB Magazine: You call it "completely novel". What do you mean by that?
S.H.: Right from the start, EtaLine Pro has been designed and developed very differently to all previous pumps. We are aiming to exceed present and future ErP Directive requirements in this way.
KSB Magazine: ErP stands for energy-related products. The corresponding directive may be better known as EU Ecodesign Directive. With the requirements stipulated therein, the European Union wants to advance climate protection. The Directive aims at saving energy and other resources when manufacturing, operating and disposing of energy-related products.
S.H.: Precisely. It is estimated that pumps account for about 10 percent of the global energy consumption – that's a huge potential.
KSB Magazine: What exactly does this mean for the development?
S.H.: The new regulations make sure that outdated power guzzlers can no longer be offered in the EU; they will be phased out – similar to what happened when classic light bulbs were banned. The commission regulation for glandless circulators came into force in 2009 and has been updated many times over the years. Naturally, it has become more stringent. I am predicting this procedure to be applied to glanded pumps as well. With the new EtaLine Pro, we are in a good position.
Testing, verifying, adjusting – the precise tuning of EtaLine Pro was a long and painstaking process.
IE? MEI? EEI? What are they and how do they apply?
KSB Magazine: In the context of energy efficiency of pumps, you often see the abbreviations IE, MEI and EEI. What do they stand for and how are they linked?
S.H.: IE stands for "international efficiency". It serves to classify the efficiency of a motor. Until recently, it ranged from IE1 as the worst value to IE4 as the best value. However, motors exceeding IE4 efficiency have been on the market for years. For this reason, the standard has been updated, and motors can now also be classified as IE5.
MEI stands for minimum efficiency index and especially refers to the hydraulic system of a water pump. To determine this index, the efficiency of different pump types in part load and overload conditions is measured and calculated with a specific formula. MEI places the measurement results in relation to the most efficient product on the market. A current MEI ≥ 0.7, for example, indicates that more than 70 percent of pumps of this type available on the market are worse in efficiency.
KSB Magazine: We have now got information on the motor and hydraulic system – but none on the complete pump yet.
S.H.: Exactly. This is the crucial point. With IE5 we have got a good motor, and an MEI of 0.7 indicates a good hydraulic system, but this is not a concise, reliable statement for the pump as an overall system. What is decisive is the overall efficiency of electric motor, hydraulic system and electronic control system – adjusted to part load requirements as the system will run in these conditions for the majority of the year.
One plus one is now more than two: The new EtaLine Pro is more than the sum of individual components.
KSB Magazine: And this is where the EEI comes into play?
S.H.: That's right. Currently, a draft of an EU regulation assesses the efficiency of glanded pumps more realistically. EEI stands for energy efficiency index. It places the electric motor input power in relation to the pump power output. In other words, how much power the pump needs to transport a specific amount of water.
KSB Magazine: How is this value determined?
S.H.: Similarly to the MEI, the EEI is a relative rather than an absolute measurement unit. Here too, reference values of the pumps available on the market are used. The value is calculated by comparing the average pump input power with the reference input power of a current standard pump. An EEI of 0.3, for instance, indicates that the pump only requires 30 percent of the power defined previously as the critical threshold value. Put simply: The lower the EEI, the less energy the pump uses. But please be aware that the EEI of a glanded pump will not be able to be compared with the EEI of a glandless pump in the future as different reference values will be used.
KSB Magazine: Okay, and how did you approach this in order to achieve the lowest EEI possible for the new EtaLine Pro?
S.H.: Well, we can see from IE and MEI that a pump is made up of very different components. First of all the centrepiece of the pump: the hydraulic system, i.e. the impeller in the casing that draws in the fluid and pumps it to the discharge pipe. Then we have got the motor driving the hydraulic system. And last but not least, modern pumps also comprise an electronic control system with sensors, variable speed control, etc.
Previously, each of these components was individually designed for optimum efficiency. So, we used to have a motor that was economical to run, an efficient hydraulic system and an optimised control unit. Each of them individually. The problem: These components have to be combined in the best possible way and they also have to harmonise with each other.
KSB Magazine: Sounds a bit like a football team…
S.H.: Exactly. You can liken it to a world-class goalkeeper, a top midfield player and a talented striker. The probability of them forming a good team is high. But it is important that the three of them play together well. I would be confident to say: A team that plays together perfectly would beat a team made up of these three individual stars. To return to the pump: We noticed that we were able to reach a very high overall efficiency with our individual components but that a perfectly matched overall system bears potential for even better results. We wanted to do away almost entirely with any adapters and interfaces that we previously required to combine the individual components. Because they cost energy too.
Development also means taking new paths
KSB Magazine: This means you had to start from scratch when designing and developing the pump.
S.H.: Absolutely. We practically started with a blank sheet. And instead of working with different teams for the various disciplines, we formed an interdisciplinary team with experts for the motor and for the hydraulic system as well as with electronics technicians, software engineers and product designers. All of them were involved right from the start.
KSB Magazine: And then it was kickoff time. How did you go about it?
S.H.: We asked ourselves what the right voltage at the internal motor terminals is and what the right rotational speed at the pump shaft, for example. We ignored outdated conventions (400 V, 50 Hz equalling 3000 rpm) in this process. A higher voltage reduces the current, for example, and in turn the mass of copper required. A higher speed lowers the torque and consequently the mass of shaft steel. That's like in Formula 1: Power can be gained from speed or engine capacity. Its higher speeds make our EtaLine Pro clearly lighter and more compact.
KSB Magazine: What was the outcome?
S.H.: The outcome felt quite disruptive compared to what we were used to: At a flow rate of 20 m³/h and a head of 30 m, for example, the CO2 emissions of the new EtaLine Pro are reduced by 43 % in production. The pump's appearance is more holistic than any of its predecessors'. Now, there is a harmonised design concept with only one display, one name plate, integrated sensors and a control unit that is modern in design and easy to operate. Everything has got a more holistic look and feel about it.
It's the inner values that count!
KSB Magazine: I am guessing that this holistic approach not only applies to production?
S.H.: It certainly doesn't. The aim was to develop a pump that not only runs highly efficiently but that meets all aspects of sustainability. We wanted to markedly reduce the number of required variants, for instance. The customer's individual requirements are met with a short delivery time and without mechanical individualisation. With "tune to process" we can give the same hardware a second or third life and extend its use phase considerably.
KSB Magazine: Not bad…
S.H.: Machinery is often excessively dimensioned "to be on the safe side". We prevent such efficiency losses. EtaLine Pro can only be operated efficiently.
KSB Magazine: Why is that?
S.H.: Because the pump with its available sensorless control modes is always demand-driven. Or it can easily and intuitively be adjusted to changed system parameters via the KSB FlowManager app. In addition, the pump offers full transparency of operating and system conditions at all times.
Compact on the outside, powerful on the inside: The new EtaLine Pro is the first pump of its type to be consistently designed for efficiency and sustainability.
KSB Magazine: Thank you very much for your explanations, Mr Horchler. To end with, let's try and take a look at the future. What are your thoughts? Can this holistic pump concept set an example for other developments at KSB?
S.H.: I think it can. Especially the approach of using an interdisciplinary team was extremely effective from my point of view. I am truly impressed by the outcome: When consistently looking at pumps as a fully intergrated systemic unit rather than a combination of individual components, there is still quite some efficiency potential to be leveraged. Energy will become more and more expensive, and sustainability more and more important. In this context I absolutely see EtaLine Pro as a pioneer, setting an example for other type series. There is still a lot for us to tap into.
KSB Magazine: Thank you very much for the interview.
Suitable products
EtaLine Pro
EtaLine Pro – more compact, flexible and efficient. Service-friendly high-efficiency variable speed in-line pump with dry-rotor permanent magnet synchronous motor. Integrated sophisticated pump functions. Well ahead of the ErP Directive's efficiency requirements. For heating and air-conditioning applications as well as water supply systems.