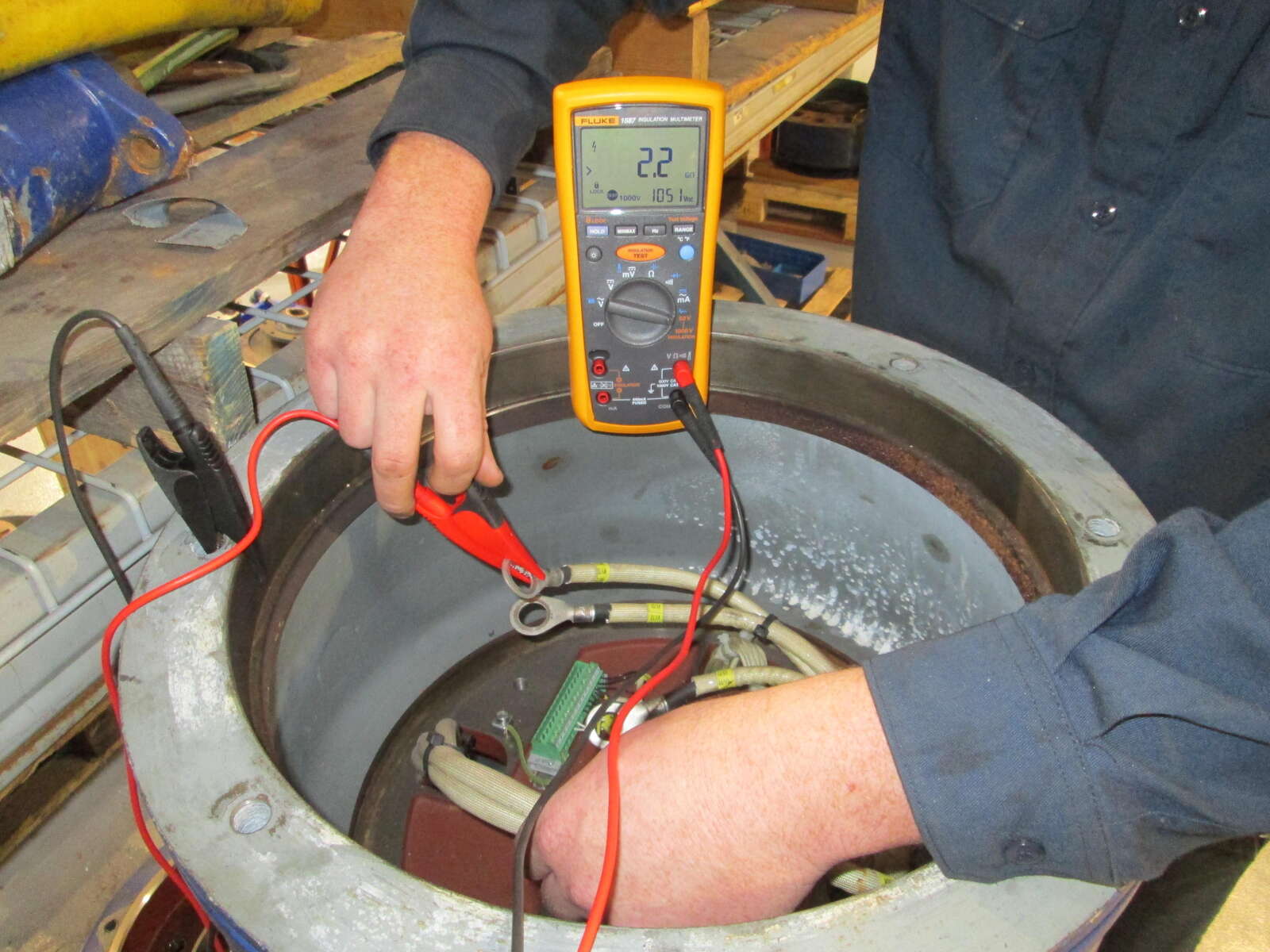
The Importance of Electrical Inspections for Pump Maintenance
Why should we make electrical inspections an integral part of our pump maintenance routine? The answer is simple: by performing electrical inspections on pumps and their systems we are able to locate faults before they become failures.
This allows the maintenance technician to plan ahead by ordering parts or replacement pumps and by scheduling system maintenance well in advance so that the pumps’ owner can avoid financially devastating downtime and costly emergency repairs. Moreover, electrical inspections can tell you many things about the overall condition of the pumping system. This is especially true for submersible pumps in which the motor and the pump are packaged as a single unit. Most pumps of these are equipped with internal sensors for winding temperature, bearing temperature and the presence of moisture. Over the last five years vibration sensors have become standard equipment in larger pumps. The information these sensors provide can make the difference between a simple rebuild or stator rewind and a complete rotor replacement.
In short, regular electrical inspections can help reduce each pump’s total cost of ownership (TCO) and make significant contributions to system reliability and uptime.
Offline testing
During a motor inspection there are several tests that are performed on the stator windings. Using a multimeter, we can test the resistance of the coils and compare them to each other. For single phase motors the resistance readings can be compared to an Ohms chart provided by the manufacturer. In three phase motors the resistance (Ohms) on each phase should be within 5%. Shorts to ground can only be found with a multimeter if there is a direct short. Other conditions, like moisture, dirt or carbonization, may not be detectable. When there is electrical arcing between the windings and ground, or between coils, the insulation of the windings becomes carbonized, basically turning the material into a semiconductor.
A semiconductor acts like an insulator until a barrier potential voltage is reached. Then the winding short behaves like a conductor. In the case of carbonized winding insulation, a multimeter cannot detect the ground fault because the test voltage of the meter (9-10vdc) is too low to reach the barrier potential of the carbonized insulation. In the past we used a hipot test to find ground shorts: a high voltage potential (2000V) is placed onto the windings and leakage through the insulation is measured to determine the condition of the insulation. Unfortunately, these testers can cause damage to the windings over time. If there is moisture or dirt present on the winding then the hipot may cause an arc to flash, instantly ruining the windings. Hipot tests are used today at the factory to determine the dielectric breakdown voltage of new windings.
A hipot test is also required for explosion-proof certification. Today we use a “Megger ™” (a trademark of the Megger Corporation) to test for shorts to ground. Megger tests work by sending a low amperage (.001A) pulse of dc voltage between the coil leads and the stator ground at two times the motor’s operating voltage (250-1000V). The Megger displays the results in mega ohms. The readings from the Megger can determine whether there is an insulation fault in the windings such as moisture, dirt or a direct short to ground. In the case of moisture or dirt the stator can be washed, dried and re-dipped in varnish, saving the owner an expensive rewind.
Megger test
For coil-to-coil and turn-to-turn shorts, multimeters and Meggers can only detect a major short. For minor shorts we need a coil and winding tester. When there is a small turn-to-turn fault, there will typically be only a tiny change on the DC resistance. With larger motors this change can be too small to detect with an ordinary multimeter. To find the short we must look at the difference between the AC resistance (inductance) and the DC resistance. While the DC resistance may change only slightly due to a minor short, the AC resistance will vary greatly with frequency. By comparing the three windings while testing over a range of frequencies, even minor shorts can be easily detected. There are two types of coil and winding testers. Both types input a low voltage AC signal and read the output. A surge tester, the most common style of coil tester, has a screen that displays the waveform as the tester steps through the frequencies. Other types calculate the differential internally and display the results on the screen.
Online Testing
The most exciting new development in the world of pump electrical maintenance is the development of online testing. This new breed of instruments can be attached to a pumping system to monitor the pump and motor while they are running. Using online testing, we can analyze the temperature, vibration, flow, pressure, power and electrical waveforms. On the motor side we can detect problems with the incoming power, bearing problems, stator shorts and dirty or wet windings. On the pump side we can measure the intake pressure, discharge pressure, fluid temperature, flow rate, bearing condition and vibration. Another feature of online testing is the ability to collect measurements over a period of time. We call this data logging. The majority of pump system problems happen when an operator is not present, the so called “ghost” failures that occur in the late hours of the night. Data logging can monitor multiple channels of information for long periods of time to capture these events as they happen. Examining data logger records collected over extended periods can also reveal trends that point to gradual deterioration of pump or motor conditions – before they become critical.
With a data logger we can also see the operating parameters of the pump system and evaluate the exact duty point and duty cycles of the system. Comparing this information with the manufacturer’s pump curves we can determine with high accuracy where the pump is operating on the curve, measure the system curve and also determine where the motor is running on the power curve. This information allows us to see the effects of pump wear, pipe restrictions and suction issues. We can also accurately calculate the pump system efficiency, which allows the engineer to offer solutions that can improve efficiency, reduce wear and decrease downtime. A great example of this is the KSB SES system, an advanced pump system data collection tool capable of monitoring complete pumping systems.
KSB SES multi-channel test equipment (Photos courtesy of KSB)
For more information about our SES system please click here
By utilizing electrical inspections during pump maintenance you can diagnose the pump system issues, offer pump owners accurate data on their pump system and find failures before they happen. The result? Better pump performance, better system availability and lower total cost of ownership.