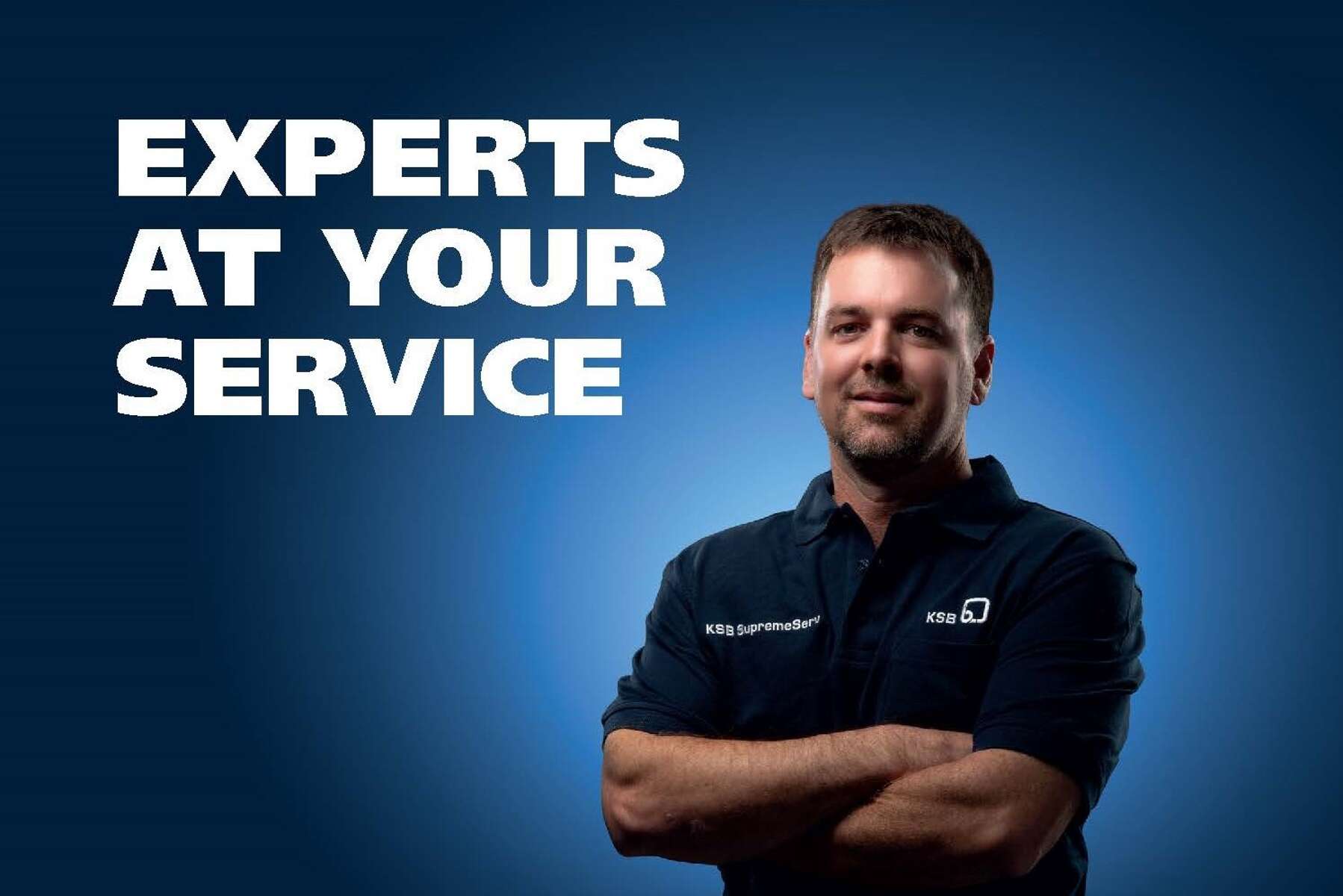
You need more than excellent products
Benefit from the extensive North American KSB SupremeServ service and spare parts portfolio. On-site or in one of our service centres located across Canada, we provide service backed by 150 years of manufacturer know-how.