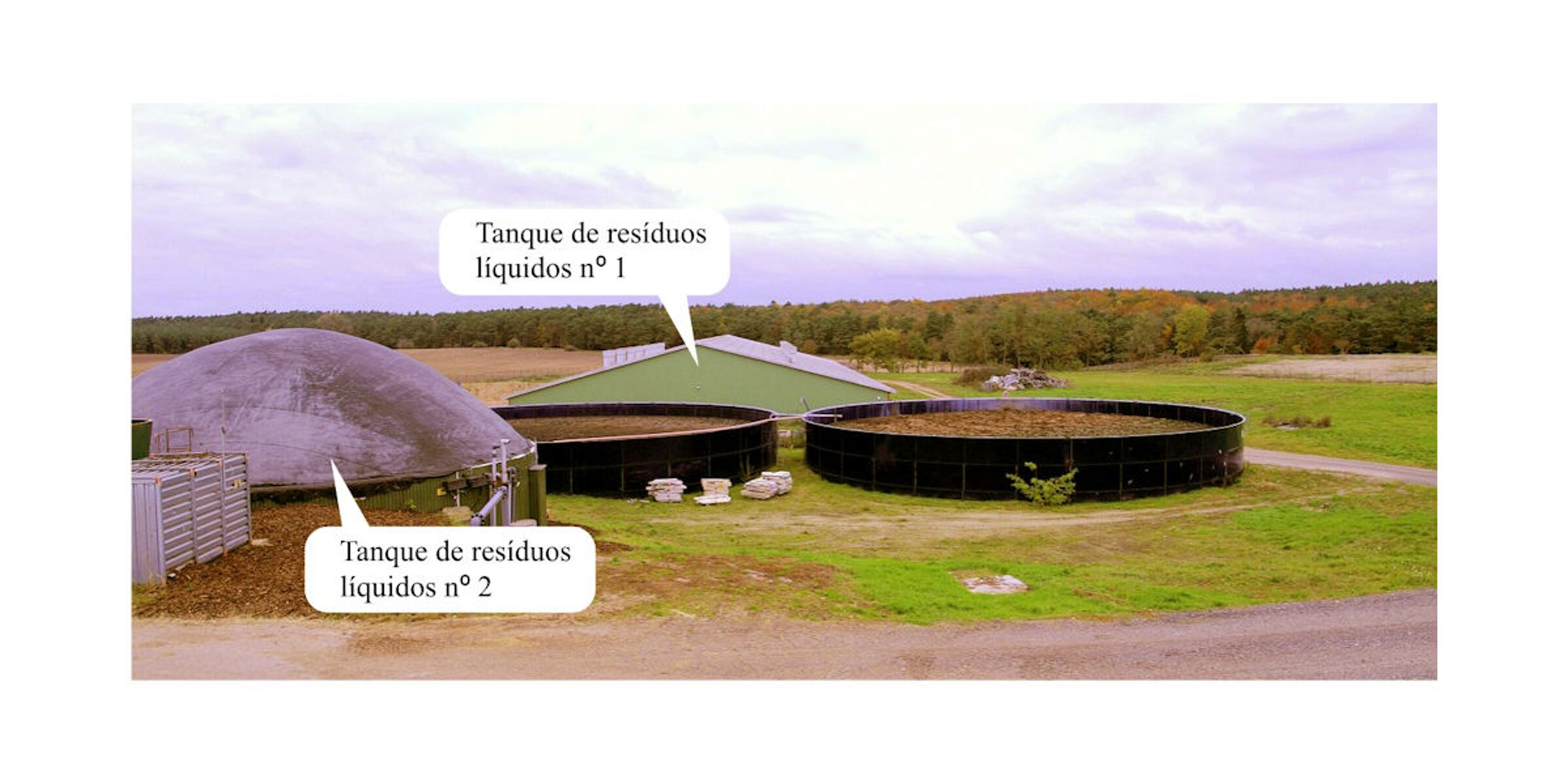
Tecnologia de agitadores na produção de biogás agrícola
O interface agro-económico
Uma quinta de gado em Baebelin, na Alemanha, especializada na criação de porcos, plantou a alimentação para os 5.000 porcos: 150 hectares de centeio e 80 hectares de milho. Esse mesmo solo fornece agora também alimento para biliões de micróbios do processo de biocenose anaeróbica, onde os materiais fitogénicos relevantes são metabolizados em depósitos cilíndricos chamados digestores.
O sistema, composto por cereais e uma biocenose reactiva, é muito sensível e exige uma homogeneização constante, realizada por agitadores. Caso contrário, os processos de fermentação microbiais que produzem o valioso – e altamente energético – gás metano, não funcionariam correctamente. O gás produzido em Baebelin, com um conteúdo de 70% de metano, será convertido em electricidade.
Grãos de cereais como fonte de energia
O agrónomo responsável por esta quinta ficou imediatamente interessado em rentabilizar os recursos energéticos do solo da quinta. Ele sabia que a área normalmente necessária para gerar 500 kW de biogás é 250 hectares. Ele também sabia, através da experiência de outros agricultores, que poderia utilizar o biogás para aquecer os celeiros, casas, estufas e turismo rural. Muitos especialistas em energia defendem as centrais bioelétricas centralizadas, com potências de pelo menos 2 MW, para tornar rentável a conversão de biogás em electricidade. Elas necessitam de enormes quantidades de biomassa, que consomem enormes quantidades de energia só para serem transportadas dos seus locais de origem para as centrais. Esse não é o caso desta quinta, porque ela cria a sua própria alimentação.
Para optimizar a produção, a rotatividade semestral das colheitas mantém o solo a produzir todo o ano. Os resíduos líquidos da produção de porcos também acrescentam energia à massa de materiais no digestor, estando em simultâneo a ser eliminados de forma não poluente. Devido a esta base favorável, este tipo de quinta é especialmente adequado para produzir biogás. Mas, apesar de tudo, a quinta ainda é mais produtora agrícola que produtora de energia, pois utiliza o dobro dos cereais para a alimentação dos porcos, do que para a produção de biogás. E, em termos de emprego, basta 1 pessoa para trabalhar na produção de energia, contra 6 na produção de porcos.
Fig. 2: Agitador de baixa velocidade da KSB, modelo Amaprop
Rentabilidade vs mecânica de fluidos
Actualmente a central de biogás converte aprox. 200 m3 de gás por hora em cerca de 400 kW de electricidade. Pelo menos metade do preço que a quinta recebe pela bioelectricidade, vai para a compra de matéria-prima. Esta central, de 450 kW, é rentável devido à grande percentagem de centeio rico em nutrientes. A rentabilidade só aconteceu depois de muitas experiências, de muitos cálculos e da minimização do consumo energético dos agitadores. O mais difícil foi optimizar o tipo de agitador submersível, dois dos quais são normalmente instalados em cada bio-reactor. Primeiro tentou-se um agitador montado lateralmente, com uma pá de grandes dimensões, rodando de forma intermitente a uma velocidade relativamente elevada, mas sem sucesso, devido à grande dimensão dos digestores. Os sólidos que flutuavam à superfície colocavam problemas, pois infelizmente o centeio de silagem (a mais importante matéria prima) é relativamente leve e propenso a flutuar, com tendência a acumular-se. Se por um lado custa menos energia apenas misturar o que fica por baixo, mais fino, na realidade não há poupanças, pois a produção de gás cai drasticamente. E, talvez ainda pior, todo o sensível sistema bioquímico pode morrer, obrigando a esvaziar todo o digestor. No final o agricultor economista compreendeu que teria de procurar ajuda em tecnologia de fluidos e engenharia de processo.
Rentabilidade vs mecânica de fluidos
Actualmente a central de biogás converte aprox. 200 m3 de gás por hora em cerca de 400 kW de electricidade. Pelo menos metade do preço que a quinta recebe pela bioelectricidade, vai para a compra de matéria-prima. Esta central, de 450 kW, é rentável devido à grande percentagem de centeio rico em nutrientes. A rentabilidade só aconteceu depois de muitas experiências, de muitos cálculos e da minimização do consumo energético dos agitadores. O mais difícil foi optimizar o tipo de agitador submersível, dois dos quais são normalmente instalados em cada bio-reactor. Primeiro tentou-se um agitador montado lateralmente, com uma pá de grandes dimensões, rodando de forma intermitente a uma velocidade relativamente elevada, mas sem sucesso, devido à grande dimensão dos digestores. Os sólidos que flutuavam à superfície colocavam problemas, pois infelizmente o centeio de silagem (a mais importante matéria prima) é relativamente leve e propenso a flutuar, com tendência a acumular-se. Se por um lado custa menos energia apenas misturar o que fica por baixo, mais fino, na realidade não há poupanças, pois a produção de gás cai drasticamente. E, talvez ainda pior, todo o sensível sistema bioquímico pode morrer, obrigando a esvaziar todo o digestor. No final o agricultor economista compreendeu que teria de procurar ajuda em tecnologia de fluidos e engenharia de processo.
Impulso optimizado e posicionamento profundo
A solução proposta pela KSB convenceu o cliente, devido à substancial redução da potência consumida: um agitador de baixa velocidade (ver fig. 2 e 3) em funcionamento permanente consome apenas 5,5% da energia que a quinta injecta na rede (e uns meros 3,5% do rendimento financeiro, devido ao subsídio por utilização de matéria prima renovável), enquanto os agitadores convencionais consomem 12%.
Fig. 3: O agitador de baixa velocidade Amaprop foi instalado longe das paredes
A primeira preocupação, e o principal aspecto qualitativo, na tecnologia de misturadores em biogás é atingir um elevado nível de homogeneização no substrato. Devido à alimentação contínua através de um parafuso de transporte, o substrato contém sempre uma certa quantidade de fibras vegetais, pelo que a homogeneização é importante não só para manter os sólidos devidamente distribuídos, mas também para garantir uma concentração altamente uniforme dos produtos metabólicos, ao mesmo tempo que mantem o pH e a temperatura favoráveis em todo o tanque.
Devem ser evitadas cavernas, ou seja, “bolsas” tipo câmaras de líquido fino na polpa, ou o habitual efeito “chávena” (partículas sólidas concentram-se no centro de um escoamento circular), bem como camadas flutuantes ou sedimentação. Estes problemas poderiam ter sido resolvidos através da distribuição de inúmeros agitadores móveis no digestor, mas isso teria sido economicamente proibitivo. Para manter o rendimento energético no mínimo, a KSB realizou uma monitorização da potência do motor e do impulso axial disponível para o processo de mistura. Esse factor é totalmente independente do rendimento do motor. O impulso produzido tem de se propagar tão longe quanto possível no tanque.
Garantir caudal base e aumentar conforme necessário
Para resolver estes problemas, a KSB utilizou um agitador de baixa velocidade, modelo Amaprop, com um diâmetro de 2,5 m. O caudal gerado por este agitador no tanque previne verdadeiramente a formação de camadas flutuantes. Além deste, foi ainda instalado um agitador de alta velocidade, modelo Amamix (ver fig. 4), no digestor principal e no pós-digestor, permitindo uma importante melhoria na homogeneização.
Fig. 4: agitador de alta velocidade da KSB, modelo Amamix
Com um motor de 16 kW, o Amamix só entra em funcionamento para ajudar a regular o processo se, por exemplo, uma parte da matéria-prima, com uma composição errada, acidificar demasiado o substrato, ou se ocorrem flutuações de temperatura inaceitáveis, causadas por falhas de electricidade ou qualquer outra situação de emergência. Os especialistas da KSB posicionaram os agitadores Amaprop e os Amamix de forma a complementarem-se, no sentido de exercerem a máxima influência possível na zona de entrada. Isto garante uma rápida mistura do fluido de entrada com o substrato existente no tanque.
Os especialistas escolheram também as posições e os ângulos de descarga dos agitadores de baixa velocidade Amaprop, de forma a aproveitar a geometria do digestor, garantindo assim a mínima resistência à propagação do impulso através do fluido. Assim, os grupos de baixa velocidade não estão instalados directamente na parede do tanque, nem junto a esta, mas a uma certa distância, bem dentro do digestor. O seu impulso é dirigido a um ponto calculado com precisão, para evitar o habitual efeito de chávena. Isso, naturalmente, evita que o material se concentre no centro do tanque.
Foto 5: Para provar a homogeneização do substrato a KSB usou uma gratícula de 9 pontos
Resultados e benefícios
De modo a documentar a poupança energética superior a 30% e a franca melhoria do efeito de mistura, a KSB analisou as propriedades bioquímicas e mecânicas de uma série de amostras do fluido do tanque, na situação inicial e na situação final. Uma consequência dessa análise foi a significativa melhoria do rendimento do processo de fermentação, o qual foi atribuído ao melhor padrão do escoamento dos agitadores KSB.
A boa mistura do digestor é um dos factores mais importantes para a sobrevivência dos microorganismos. Adicionalmente a utilização de 2 agitadores de baixa velocidade é claramente mais económica que a utilização de 4 agitadores de alta velocidade, em cerca de 11.000 euros por ano (ver tabela).
Esta comparação baseia-se num impulso produzido de 8.500 N e num preço da energia de 0,1€/kWh. O dono da quinta acrescenta que a manutenção dos agitadores é fácil (basta elevá-los para fora do tanque sem ter de o esvaziar, de 16.000 em 16.000 horas de funcionamento ou de 2 em 2 anos) e que as obras de aumento da capacidade (para 500 kW) lhe vão permitir abastecer de energia um novo cliente, um hotel, para aquecimento das piscinas, restaurantes e quartos – tudo numa base ecológica de matérias-primas renováveis produzidas localmente !
João Leite / Director Geral