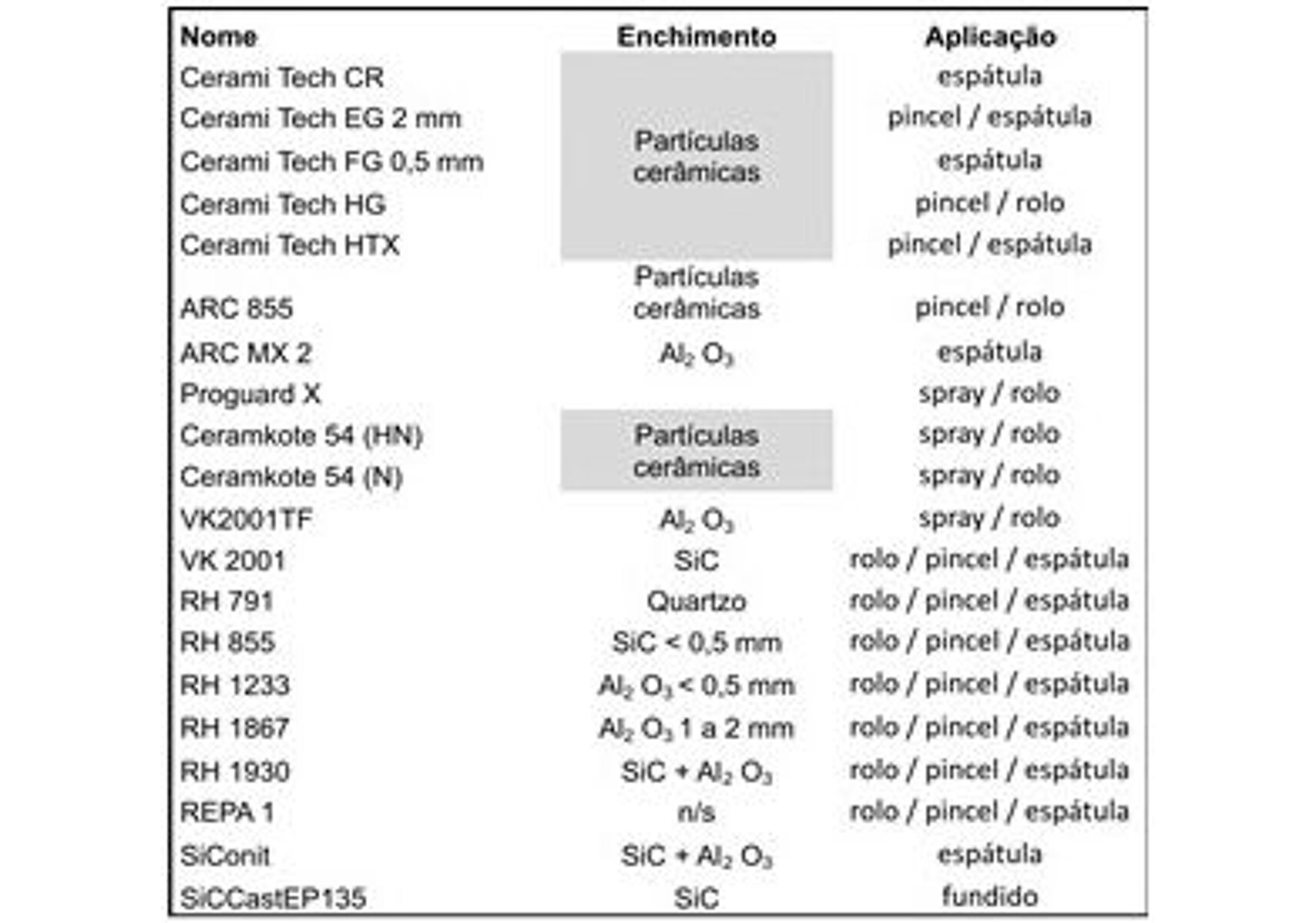
Estudo da resistência de revestimentos
Existe no mercado um elevado número de produtos para revestimentos cujos fabricantes reclamam como tendo propriedades de redução dos efeitos da corrosão e do desgaste abrasivo. Os fabricantes de equipamentos tem utilizado esses produtos numa base experimental por forma a constatar se, na prática, algum desses produtos realmente ajuda na performance dos seus equipamentos, ao proporcionar-lhes uma maior resistência ao desgaste abrasivo, cavitação e/ou corrosão.
1 – Revestimentos testados, à base de resina epóxica
A KSB decidiu, através da realização de uma série de testes nos seus laboratórios de materiais, avaliar a qualidade dos revestimentos, tentando com isso, mais claramente, avaliar as reais capacidades destes, no que se refere à sua aplicação a bombas centrífugas.
Os materiais das bombas centrífugas, estão sujeitos a esforços muito complexos. A concepção estrutural e hidráulica de um determinado componente considera os esforços mecânicos e térmicos a que o mesmo vai estar sujeito. Adicionalmente, todos os componentes em contacto com o fluido estão sujeitos às propriedades desse mesmo fluido. Dependendo das características deste, podemos estar perante efeitos de corrosão, abrasão e/ou cavitação, os quais irão afectar os componentes da bomba.
O ferro fundido e os aços de baixa liga são materiais habituais em aplicações de águas de abastecimento público, águas residuais e circuitos de arrefecimento – sendo os principais critérios da sua selecção o preço, a facilidade de construção e a disponibilidade. No entanto, devido às suas limitações de resistência e durabilidade, estes materiais rapidamente atingem os seus limites quando na presença de fluidos abrasivos e/ou corrosivos, originando danos nos principais componentes hidráulicos das bombas (impulsores e volutas). Por forma a evitar a utilização de materiais mais dispendiosos – os aços inoxidáveis – o mercado normalmente disponibiliza uma série de revestimentos (ver fig. 1) como solução alternativa a estes problemas. É, contudo, difícil encontrar no mercado um revestimento adequado a muitas situações, pois existem várias condições que têm que ser simultaneamente satisfeitas.
Critérios principais na selecção dos revestimentos
- Resistência química ao fluido, à temperatura de serviço.
- Possibilidade de aplicação do revestimento em toda a geometria do componente
- Aprovação do revestimento para água potável (nessa aplicação)
- Facilidade de maquinagem nas superfícies de vedação e nas zonas com folgas funcionais.
Para os utilizadores dos revestimentos, o principal problema é encontrar de entre tantas marcas e tipos de revestimento disponíveis no mercado, aquele que mais se adequa à sua aplicação em concreto. Os fabricantes de revestimentos utilizam normalmente um vocabulário muito apelativo, como “extremamente resistente à abrasão” ou “eminentemente resistente à corrosão” ou “ resistente à cavitação”, entre outros, mas todos eles pouco ajudam ao fim pretendido. Para que, realisticamente, se possa avaliar a aptidão destes revestimentos na sua utilização em componentes das bombas centrífugas, a KSB sujeitou alguns destes revestimentos a testes de abrasão e cavitação.
Com base na sua composição orgânica, os revestimentos podem ser agrupados em duas categorias: resinas epóxicas e poliuretanos.
Revestimentos à base de resinas epóxicas
A maioria dos revestimentos analisados pertence a este grupo. Para aumentar a sua capacidade de resistência à abrasão, estas resinas são misturadas com partículas de cerâmica dura, como alumina, carbonetos de silício, ou equivalente.
Individualmente, os vários tipos diferem pelo tipo de resina epóxica, pelo tipo de “endurecedor” e pela natureza, quantidade e distribuição da sua “componente dura”. O “endurecedor” é normalmente misturado na resina epóxica imediatamente antes da aplicação. Após aplicado, o revestimento normalmente endurece à temperatura ambiente. A aplicação do revestimento pode ser efectuada por spray, com pincel, com espátula ou com rolo. Uma vez que contêm componentes cerâmicos, os seus fabricantes atribuem-lhes erradamente a designação de “revestimentos cerâmicos” o que não é rigoroso. Nas figuras 2 a 4 podemos observar exemplos típicos destes revestimentos.
Na fig. 2 apresenta-se a matriz de um revestimento típico de aplicação com pincel. Entre algumas partículas maiores (100 mm) e bolhas esféricas de ar, vemos nesta matriz muitas pequenas partículas cerâmicas. A espessura da camada de aplicação é normalmente de várias centenas de mícrones. As matrizes dos revestimentos apresentados nas fig. 3 e 4 contêm um maior número de partículas cerâmicas (com alguma dimensão), pelo que necessariamente tem que ser aplicadas por espátula. Devido a dimensão, relativamente grande, destas partículas a espessura da camada de aplicação deve ser de, no mínimo, 3 mm.
Revestimentos à base de poliuretano (PU)
Os revestimentos à base de poliuretano são normalmente aplicados por spray, com pincel ou moldados, dependendo da sua formulação e tipo de aditivos utilizados. O poliuretano, sem partículas sólidas, é frequentemente utilizado na prevenção do desgaste abrasivo. Tal como nos vedantes à base de borracha, a sua elasticidade promove o amortecimento da energia cinética oriunda do impacto dos sólidos na sua superfície, reduzindo assim o desgaste por abrasão.
Foram analisados dois tipos de revestimento à base de poliuretano (ver fig. 5):
- Revestimentos à base de PU reforçados na fase dura (semelhantes aos revestimentos de resina epóxica)
- Revestimentos à base de PU sem reforço na fase dura (semelhantes aos vedantes de borracha)
Fig. 5 – Revestimentos testados, à base de poliuretano
Resistência ao desgaste abrasivo e à cavitação
Foram realizados ensaios de abrasão e cavitação para avaliar a capacidade de resistência de cada um dos revestimentos a estes fenómenos.
Ensaio de abrasão: foram efectuados testes com jacto de água + areia (contendo quartzo com granulometria de 80 mm) a uma velocidade de 15 m/s e um ângulo de impacto de 45º.
Após os ensaios foi avaliado o rácio de desgaste por unidade de energia (mm3/kJ), em função da massa perdida por cada amostra.
Como a experiência demonstra que o nível de desgaste nos revestimentos depende do tempo de exposição ao desgaste, para obter rácios de desgaste comparáveis, alguns revestimentos foram analisados uma 2ª vez, após 2 horas de desgaste adicional.
Este fenómeno (dependência do tempo de exposição) resulta do facto dos polímeros – devido à sua elasticidade - serem erodidos, ficando a sua superfície alterada. Só quando as partículas duras (cerâmicas) estão completamente livres e à vista é que se observa efectivamente o efeito de resistência ao desgaste. Os compostos mais pastosos, contendo maiores quantidades de partículas duras, conferem manifestamente uma maior dependência do tempo de exposição.
Resultados dos testes
As figuras 6 e 7 apresentam os resultados obtidos no teste com jacto de areia a que cada uma das amostras dos revestimentos foi sujeita. Para efeitos comparativos foram incluídos os rácios de desgaste dos materiais KSB: Norihard®(NH 153), Noricrom® (1.4475), Noridur®
Figura 7 – Resultados obtidos no teste com jacto de areia, quer no 1º ensaio (15 m/s, 45º, 80 mm), quer no 2º ensaio de alguns revestimentos (mais 2h de ensaio, nas mesmas condições), representado pelas linhas a azul claro. Valores em mm3/kJ. (1.4593) e ferro fundido cinzento GJL-250 (JL 1040).
Conclusões
Os revestimentos para aplicação a pincel – mais líquidos – são efectivamente mais fáceis de aplicar e apresentam um comportamento diferente dos anteriores, pois mantêm desde o início o seu nível máximo de resistência à abrasão. Isto significa que as pequenas partículas duras oferecem uma pequena resistência. De entre os revestimentos à base de poliuretano, os puros (sem qualquer adição de materiais duros) são os que apresentam os níveis de desgaste mais baixos, mas as variedades com partículas duras têm ainda assim resistências ao desgaste substancialmente superiores aos revestimentos à base de resinas epóxicas.
Alguns revestimentos, apresentados na figura 8, mostraram níveis de desgaste reduzido, semelhantes aos do ferro fundido cinzento.
Fig. 8 – Revestimentos com rácios de desgaste semelhantes aos do ferro fundido cinzento, GJL-250 (JL 1040)
As conclusões gerais podem ser assim identificadas:
- A resistência à abrasão dos diferentes tipos de revestimento varia muito
- Na maioria dos casos os níveis de resistência ao desgaste são inferiores aos do ferro fundido cinzento GJL-250 (JL 1040)
- Nenhum dos revestimentos se aproxima dos níveis de resistência ao desgaste obtidos com os materiais Norihard®(NH 153) e Noricrom® (1.4475), da KSB.
A interacção da corrosão com a abrasão
Não deve no entanto, ser esquecido, para uma interpretação adequada das conclusões obtidas, que:
- Os ensaios foram efectuados apenas comparando a influência de um jacto de areia e água.
- Não foram tidos em consideração os efeitos da corrosão na análise do desgaste abrasivo.
Nestas condições o resultado do ensaio de desgaste do Noridur®(1.4593) é apenas ligeiramente inferior ao do ferro fundido GJL-250 (JL 1040) – o que vai totalmente contra o que se verifica na prática. A experiência demonstra que, em muitos casos de desgaste abrasivo, os componentes em ferro fundido são substituídos por componentes em aço inoxidável. Isto porque os componentes das bombas estão sujeitos a inúmeros outros factores (corrosão, caudal contínuo, cavitação, diferentes tipos de sólidos, etc.), que contribuem conjuntamente para o desgaste dos materiais.
No caso específico do ferro fundido, a corrosão é de fundamental importância. A bombagem de fluidos - ainda que ligeiramente - corrosivos leva a que frequentemente ocorram danos de corrosão/abrasão nos impulsores das bombas centrífugas. O revestimento superficial protector do material é mecanicamente destruído por desgaste e leva a que o metal seja rapidamente corroído.
Em conclusão, face aos resultados obtidos, a KSB recomenda que sejam convenientemente avaliadas as características do fluido (sua composição e características) e o tipo de funcionamento previsto para o equipamento (existência de cavitação, velocidade de rotação, velocidade de escoamento) antes de se optar pela selecção do tipo de revestimento a aplicar, pois corremos o risco de estar a efectuar um revestimento do qual poderemos não obter qualquer proveito em termos de vida útil do equipamento.
Paulo Costa / Resp. Depto. Indústria