Shaft coupling
The shaft coupling is the connecting element between the electric motor and the pump hydraulic system. Slip-free shaft couplings employed in centrifugal pumps are divided into rigid and flexible shaft couplings.
Rigid shaft coupling
Rigid shaft couplings are mainly used to connect perfectly aligned shafts. The slightest misalignment results in considerable extra stress on shaft couplings and adjoining shaft ends.
Examples of rigid shaft coupling types
- Sleeve coupling
- Muff coupling
- Serrated (splined) coupling
- Split muff coupling (DIN 115)
- Disc coupling
- Flange coupling
- Gear coupling
Flexible shaft coupling
Shaft couplings to DIN 740 are resilient (flexible), slip-free connecting elements fitted between driving and driven components, capable of partially compensating axial, radial and angular misalignment and shock loads.
See Fig. 1 Shaft coupling
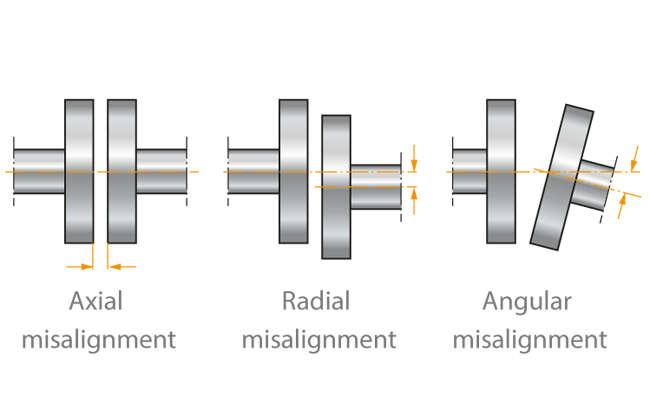
Fig. 1 Shaft coupling: Misalignment types
Flexibility is usually achieved by the deformation of dampening, rubber or metal-elastic spring elements; their service life is heavily dependent on the extent to which misalignment has to be compensated. Different flexible shaft coupling designs are available.
See Fig. 2 Shaft coupling
-data.jpg?ci_url_encoded=1&force_format=webp&q=60)
Fig. 2 Shaft coupling: Coupling types
If shaft misalignment occurs between the driver and the pump as a result of, for example, temperature fluctuations in the fluid handled (on heat transfer and hot water pumps) the double-cardanic coupling type design is often employed.
See Fig. 3 Shaft coupling
-data.jpg?ci_url_encoded=1&force_format=webp&q=60)
Fig.3 Shaft coupling: Double-cardanic coupling for compensating shaft offset
Gear couplings are flexible shaft connections for positive torque transmission and are particularly suited to compensating axial, radial and angular shaft offsets.
The design principle employed by curved-tooth gear couplings (see Curved-tooth gear coupling) prevents edge pressure when gears engage in the case of angular and radial offset, making these couplings almost wear-free.
The double-cardanic operating principle of curved-tooth gear couplings ensures that the reaction forces from angular and radial offsets are negligible and periodic fluctuations in the angular velocity do not occur.
See Fig. 4 Shaft coupling
-data.jpg?ci_url_encoded=1&force_format=webp&q=60)
Fig. 4 Shaft coupling: Curved-tooth gear coupling
A coupling with spacer sleeve (see Back pull-out design) allows the shaft seal and pump bearing assembly to be removed without removing the pump casing and the drive.
See Fig. 5 Shaft coupling
-data.jpg?ci_url_encoded=1&force_format=webp&q=60)
Fig. 5 Shaft coupling: Spacer-type coupling
If precise data on the influence of the frequency of starts and the ambient temperature is not available, the load can be calculated on the basis of factors specified as reference values. No fixed value is laid down for the ratio of maximum torque to operating torque. This means that all coupling types can be taken into consideration according to their specific suitability. The calculation of the loading by torque shocks relates therefore to the maximum torque (see Starting torque).
The calculation method for sizing flexible couplings given in DIN 740 only applies on the assumption that the coupling is the sole torsionally flexible element of a rotor, reducing the installation to a linear two-mass system. In all other cases it is necessary to carry out a vibration calculation.