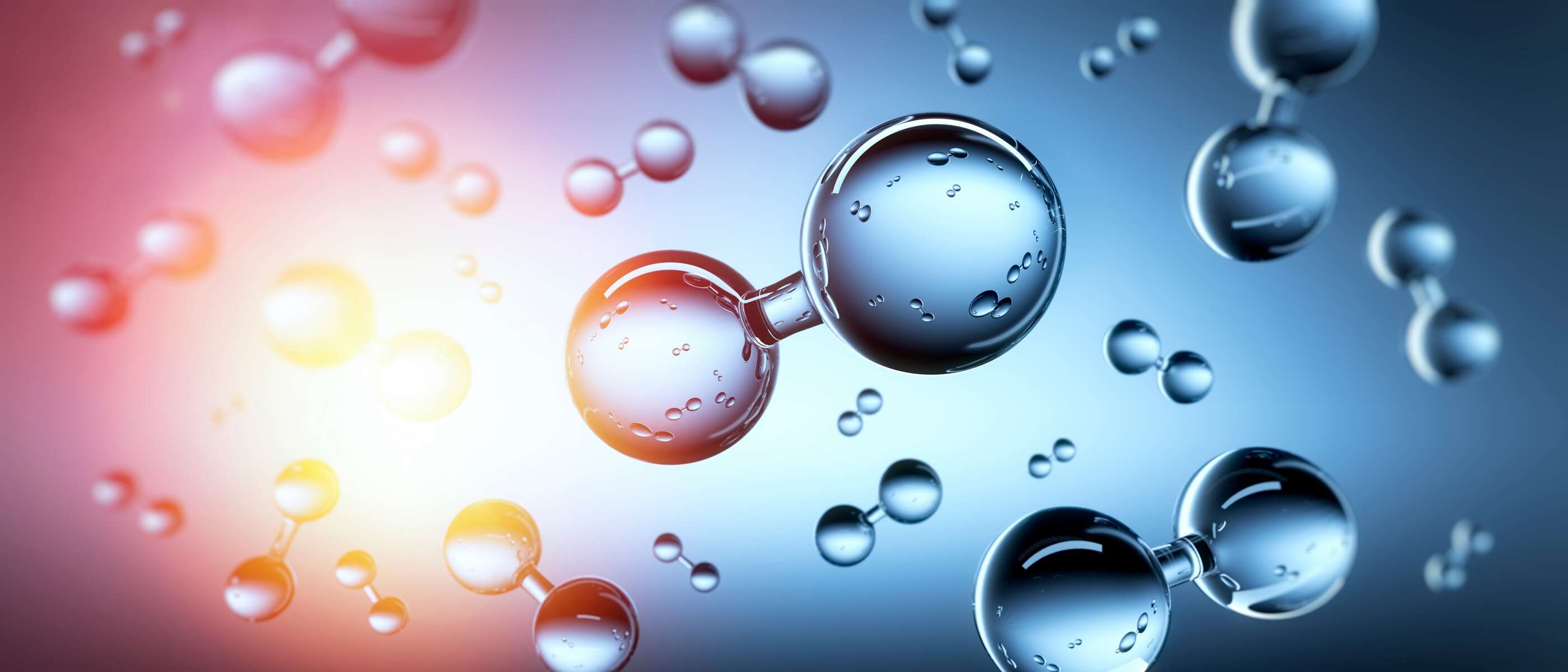
PEM electrolysis: Key questions and answers
Green hydrogen is a cornerstone of energy transition and decarbonisation in many industries. PEM electrolysis plays a major role in its production. What are the benefits of this technology, and what challenges have to be overcome? How is it used and further developed? We provide answers to key questions.
What is PEM electrolysis?
PEM electrolysis is a process used for producing hydrogen. In this process, water is split into hydrogen and oxygen in an electrolyser with the help of electricity. The technology involved is named after a membrane that plays a central role in splitting the water: the proton exchange membrane, PEM. The membrane is usually made of the polymer Nafion and has got a special property: It is permeable to positively charged particles but not to negatively charged or neutral ones.
In a PEM electrolyser, this membrane is located in a chamber filled with water. Two electrodes are fitted on opposite sides of this chamber: the positive anode and the negatively charged cathode. Voltage is applied to split the water. The anode attracts the negatively charged electrons of the water molecules and splits them into hydrogen nuclei (protons) and oxygen atoms. As the hydrogen nuclei are lacking their electrons, they are now positively charged ions.
This is where the special property of the membrane comes into play: It makes the positively charged hydrogen nuclei move to the cathode side and thus separates them from the electrically neutral oxygen atoms. On the other side of the membrane, the negatively charged cathode releases electrons to the hydrogen nuclei, which turns them into complete, electrically neutral hydrogen atoms.
They are discharged and collected and can be used for myriad applications: as a base material for the chemical industry, for storing electricity or as fuel for fuel cell vehicles, for instance.
What role does PEM electrolysis play in the energy transition?
Hydrogen is referred to as "green" if it is produced without any carbon dioxide emissions by using regenerative power sources, such as wind or solar energy. Green hydrogen is seen as a cornerstone of the energy transition. By now, 43 countries have developed national hydrogen strategies to promote its use. The US government, for example, stated its intention in the U.S. National Clean Hydrogen Strategy and Roadmap to generate 50 million tonnes of green hydrogen a year by 2050. According to the EU's hydrogen strategy, the EU is to generate 10 million tonnes from renewable energies by 2030 and import the same quantity again from partner countries.
One of the challenges of using wind and solar power for hydrogen production is that these energy sources are weather-dependent and therefore do not provide a constant output. Often, at times with a lot of wind or sunshine, more power is produced than consumed. The opposite are "dark lulls", which are phases with little sunshine and no wind.
PEM electrolysers are comparatively flexible systems that can be started up quickly, reliably produce hydrogen also at low loads, and respond swiftly to any changes in power supply. This makes them ideal for using excess power from renewable energy sources, such as wind and solar energy, to produce hydrogen. During dark lulls the hydrogen produced can be reconverted into electricity to stabilise the power supply networks. Despite PEM electrolysers currently only making up 22 percent of the electrolysis capacity installed worldwide, they play an important role in the energy transition due to their special properties.
How is a PEM electrolyser structured?
Decentralised PEM electrolysers are typically installed in containers. They are package systems that are fast to commission and can be upscaled to larger systems.
The core component of a PEM electrolyser is the stack, in which the water is split. Depending on the size and application, a stack contains between 30 and 220 electrolysis cells, stacked and connected in series. Each cell contains a membrane as well as the electrodes.
The stack is supplied with water via a circuit. Ultra-pure water is used for PEM electrolysis because contamination, such as dissolved metals, ions or organic substances could otherwise block the fine pores of the membrane or impair the electrodes' performance.
The water is introduced into the electrolysis cells of the stack on the anode side. After the electrolysis, it leaves the stack as a mixture containing oxygen. The oxygen is then largely removed by a gas separator. Then, the water temperature is reduced by a heat exchanger that is connected to evaporation coolers via a cooling circuit. A pump transports the water back to the stack. The circuit always uses up some water, splitting it into hydrogen and oxygen. This water is continuously replenished through integrated water treatment and pressure generation systems, which maintain a constant pressure within the circuit.
The hydrogen generated is collected on the cathode side of the cell, freed from residual water, cooled and then stored.
A pressure difference exists between the electrolysis cell's anode side producing oxygen and its cathode side producing hydrogen. The circuit on the anode side works at atmospheric or slightly higher pressure; on the cathode side the pressure is 15 to 30 bar. The main reason is that hydrogen has to be stored under pressure in order to be used. The increased system pressure does away with the need to fit further systems downstream to compress the hydrogen. This makes the system less complex.
Electrolysis usually takes place in the range of 50 °C to 80 °C. This temperature enables efficient proton conduction. At the same time, the temperature is not hot enough to damage the sensitive membrane, which could become deformed by higher temperatures.
The extreme conditions in the stack during electrolysis present significant challenges for the components. Hydrogen ions create an acidic, aggressive environment with a pH below 2, corresponding roughly to the value of gastric juice or battery acid. This is why this process is sometimes also called "acidic" electrolysis. The electrodes have to be made of precious metals, such as platinum and iridium, that are corrosion-resistant and act as catalysts.
The ultra-pure, deionised water also corrodes metals. As it contains an extremely low concentration of dissolved ions, it tends to remove ions from metal surfaces, corroding the surfaces in this way.
To drive the processes in a PEM electrolyser, numerous pumps and valves are required. They supply the electrolyser with treated water and the required pressure, ensure an even circulation through the stack and provide the optimum temperature for operation. Given the aggressive environment, manufacturing electrolysers requires a vast amount of know-how regarding materials and surface treatment to minimise corrosion as much as possible.
How does PEM electrolysis differ from alkaline electrolysis (AEL)?
Alkaline electrolysis is the oldest electrolysis procedure and has been used industrially since the early 20th century. About 60 percent of the electrolysers installed worldwide are based on alkaline electrolysis, according to the International Energy Agency (IEA). By comparison: Only 22 percent of electrolysers worldwide use PEM electrolysis.
PEM electrolysis creates a very acidic environment, whereas alkaline electrolysis takes place in basic conditions. Potassium hydroxide of a concentration of 20 to 40 percent is added to the water. This produces negatively charged hydroxide ions consisting of one hydrogen atom and one oxygen atom.
If a voltage is applied, the negative hydroxide ions travel to the positive anode. This is where they release electrons and form water and hydrogen. At the negative cathode, the water molecules take on electrons and dissociate into hydrogen and new hydroxide ions.
A porous wall separates the anode side from the cathode side and ensures that the hydrogen and oxygen cannot mix. As the alkaline environment is less corrosive than the acidic environment of PEM electrolysis, no precious metals are needed for the electrodes. Comparatively low-cost metals, such as nickel, are used for the electrodes in alkaline electrolysis.
The electric efficiency of alkaline electrolysers is similar to that of PEM electrolysers at 60 to 80 percent. However, alkaline electrolysers need to be significantly larger to produce the same output. The reason behind this is that they have to be operated at a markedly lower current density (the amount of current per unit area of an electrode surface) as the basic solution of alkaline electrolysis is not as conductive as the membrane of PEM electrolysis. Higher currents would also increase energy losses and lower the efficiency of the system. In addition, heat would be generated that may impact the longevity of the electrolyser.
What are the benefits of PEM electrolysis?
PEM electrolysis offers a number of benefits compared to alkaline electrolysis, which makes it a key technology for green hydrogen production and the energy transition.
What are the disadvantages of PEM electrolysis?
Next to its benefits, PEM electrolysis has also got some disadvantages that need to be considered in its application.
What is the role of pumps and valves in PEM electrolysis?
Pumps and valves control numerous processes in PEM electrolysers. Their quality plays a crucial role in the efficient long-term operation of systems. First of all, they have to be corrosion-resistant to contribute to a long electrolyser life. Also, pumps and valves that have not been designed for electrolysis can add ions and other contamination to the water. This may damage the membrane and impair the efficiency and longevity of the system.
KSB therefore manufactures its components for electrolysers of high-grade steels, observing high quality standards. To prevent contamination of the stack with ions, the company cleans all surfaces and treats them by applying a KSB-developed procedure. KSB offers a broad range of pumps and valves, covering the requirements of systems of all sizes. Some typical applications:
What will the future development of PEM electrolysis look like?
For green hydrogen to be successful on the market, it is crucial to become more cost-efficient. It has to become competitive with the so-called “grey” hydrogen, that is generated from natural gas and emits carbon dioxide in the process.
According to information from Bloomberg, in 2023 the average cost of green hydrogen was US$ 6.4 per kilogram, compared to US$ 2.13 per kilogram for grey hydrogen.
A large share of research in the field of PEM electrolysis therefore aims at lowering the investment and operating costs. A particular focus is on reducing the quantity of precious metals in the electrodes. Further objectives are to lower the efficiency degrading of the stack, optimise the conductivity of PEM layers for protons, and increase the current density with more robust materials to enhance efficiency.
These priorities are also reflected in research funding: Clean Hydrogen Partnership, an initiative for funding hydrogen research by the EU Commission, the EU and the hydrogen economy is planning to lower the quantity of precious metals for PEM electrolysers from currently 2.5 milligrams per watt of power intake to 0.25 milligrams per watt by 2030. Efficiency degrading is to be reduced from 0.19 percent per 1000 operating hours to 0.12 percent, and the power input per kilogram of hydrogen from 55 to 48 kilowatt hours. Similar targets have been set by the US Hydrogen and Fuel Cell Technologies Office for its research funding in the USA.
How does KSB support its customers with electrolysis projects?
The quality of pumps and valves is decisive for an efficient, long-term operation of electrolysers. Optimally selected components extend the service life of electrolysers and ensure a high system efficiency. As a market leader KSB can supply top quality by drawing on decades of experience in working with the chemical industry.
In this way, KSB employees have gained detailed knowledge of systems engineering, operating modes, materials and energy efficiency, which the company makes available to support and consult its customers. This is illustrated by numerous reference projects, both in the field of PEM electrolysis and in that of alkaline electrolysis.
To better understand the demands and requirements and keep developing our products, KSB’s experts not only work closely with their customers and the work groups of standardisation organisations. They also do their own research in test facilities, investigating the behaviour of liquids and gases in the most diverse of mixtures and temperatures that may occur in real life.
As a full-range supplier, KSB offers a portfolio that covers all phases of the hydrogen value chain. For instance, the company not only supplies pumps and valves for generating hydrogen in the electrolyser, but also for storage and transport. KSB's portfolio covers all applications and system sizes, no matter whether PEM electrolysis, alkaline electrolysis or future technologies, such as anion exchange membrane electrolysis.