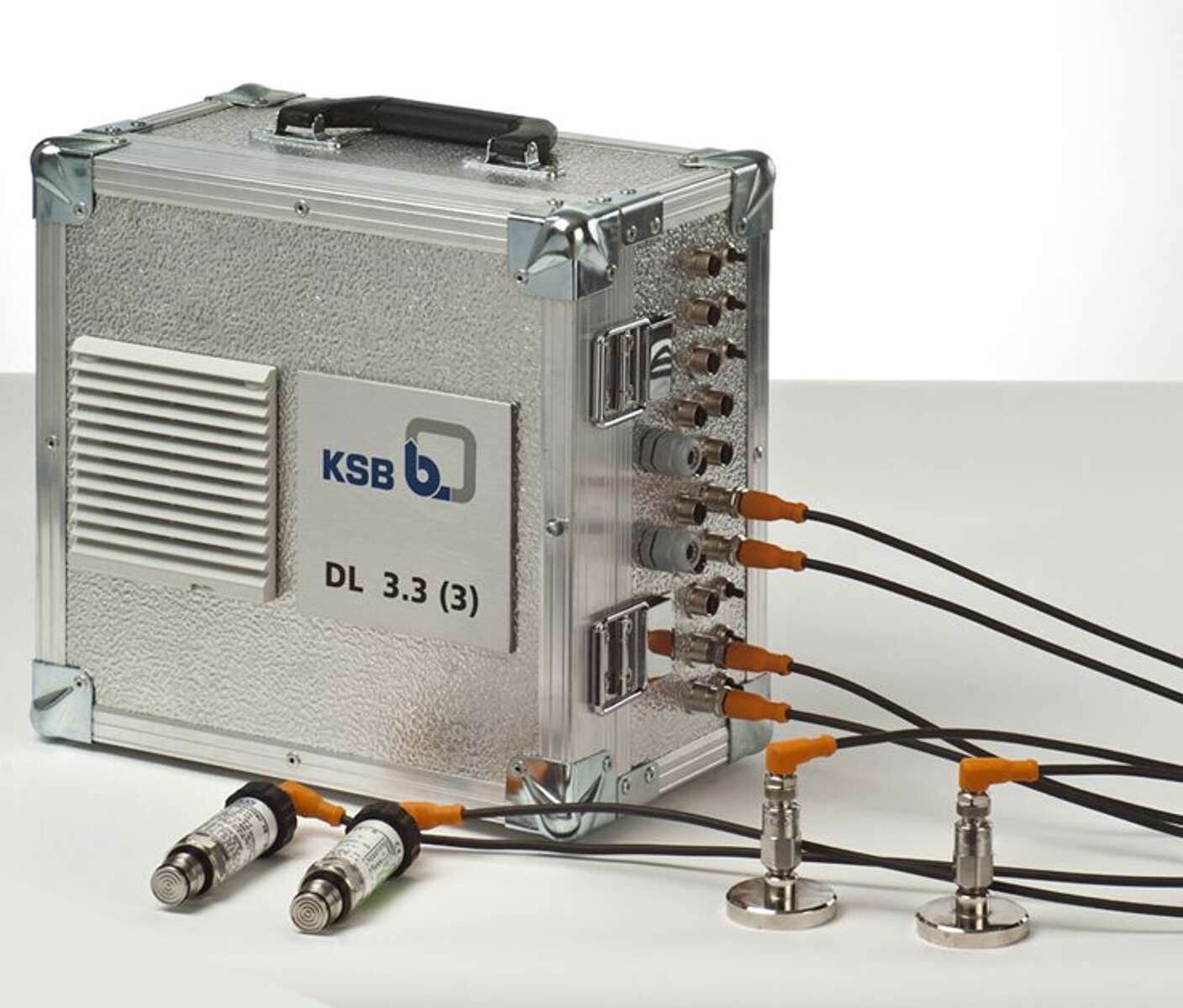
On-site Testing of Pumps
As was pointed out in a previous article, the key to minimizing the cost of operating pumps lies in making a good match between each machine’s performance characteristics and the requirements of the system where it is installed.
Having pumps operate at or near their ‘best efficiency point’ (BEP) not only improves overall energy efficiency, but also results in smoother running, lower maintenance costs, fewer outages and longer pump lifetimes. (See Figure 1) However, in complex systems, predicting system characteristics over a full range of operating conditions can be very difficult. Moreover, plant modifications, changes to the operating profile or even the slow accumulation of solids and build up inside pipes can have significant effect on system characteristics. In practical terms it can be extremely valuable to evaluate pumps’ performance in the field in order to make well-informed decisions about system operations and the potential for energy and cost savings.
Figure 1: The relationship between pump reliability and operating conditions
On-site testing
On-site testing tools can be attached directly to a pumping system to monitor the pump and motor while they are in operation and analyze characteristics such as pressure, flow rate and fluid temperature at multiple locations around the piping system. The pumping set can be monitored to determine vibration levels, power consumption and rotation speed under various operating conditions. Putting all this information together makes it possible for an experienced technician to analyze the performance and head off potential failures.
Some pumps, especially larger units, have built-in sensors that measure vibration, moisture and temperatures at critical points on bearings or motors. These can be very helpful in heading off problems that could result in damage to the pump or motor. In general though, extra instruments – including pressure and flow monitors – are needed to conduct a full on-site assessment of the pump system.
An essential feature of modern on-site testing techniques is the ability to collect measurements over a period of time. This is called data logging. Many pump system problems happen when an operator is not present, the so-called ‘ghost’ failures that occur in the late hours of the night. Data logging can monitor multiple channels of information for long periods of time to capture these events as they happen. Examining data logger records collected over extended periods can also reveal trends that point to a gradual deterioration of pump or motor conditions before they become critical. With a data logger, it is also possible to measure the parameters of the pump system over a range of operating conditions and to evaluate the exact duty point and duty cycles of the system. By comparing this information with the manufacturer’s pump curves, an experienced technician can determine with a high degree of accuracy the operating point of the pump as commanded by the system. This analysis in conjunction with on-site inspections can help determine performance deteriorating effects like pump wear, pipe restrictions and intake suction issues.
KSB System Efficiency Services
KSB’s SES (System Efficiency Services) is a specialized service offering that makes the best use of data collection tools capable of monitoring complete pumping systems. Collecting the data is not the challenge; it is in the interpretation and analysis of the data where the true value lies. The combination of accurate, relevant system performance data and KBS’s knowledge and experience make it possible to diagnose problems and find solutions that can improve efficiency, reduce wear and decrease downtime. The quantitative data from on-site measurements can also be used to build a business case for making system changes that will improve operating efficiency.
Case Studies
Wastewater pumping station
Figure 3: Waste water pumping station
The operators of a wastewater treatment plant found that several submersible pumps in an inlet tank were suffering from extreme vibration and premature failure. An SES investigation discovered that the most severe vibrations were occurring when water levels in the tank were relatively low. Under these conditions, the pumps were drawing in a mix of water and gas. The solution was to install a curtain wall around the pumps so that the water near the pump intakes was calmer and contained less entrained gas. Replacement pumps were also right-sized for the application, resulting in an improvement in pump efficiency.
Costs saved by SES | Pump1 | Pump 2 |
Energy costs per annum prior to optimization | $17,634 | $19,676 |
Energy costs per annum with ew pump | $13,441 | $13,565 |
Savings per annum | $ 4,194 | $ 6,110 |
Cost of two new pumps | $21,120 | |
Payback Period | 2 Years |
Cooling water circuit of a chemical plant
Figure 4: Chemical plant
In this case, an SES investigation discovered that the pumps powering a cooling water circuit in a large chemical plant had been over-sized for normal operations. In an emergency, the cooling system would be called upon to deliver up to 400 cubic metres of water per hour for firefighting. However, 300 m3/h would meet normal operating requirements. The recommended solution involved replacement of the existing pumps and the installation of variable speed drives so that the flow capacity of the pumps could be varied to meet all requirements.
Costs saved by SES | |
Energy costs per annum prior to optimization | $59,681 |
Energy costs per annum using speed control | $44,544 |
Savings per annum | $15,106 |
Cost of two new pump sets | $27,866 |
Payback period | 1.84 years |
Energy saved | 100,000 kWh |
Reduction of CO2 emissions | 62 tonnes |