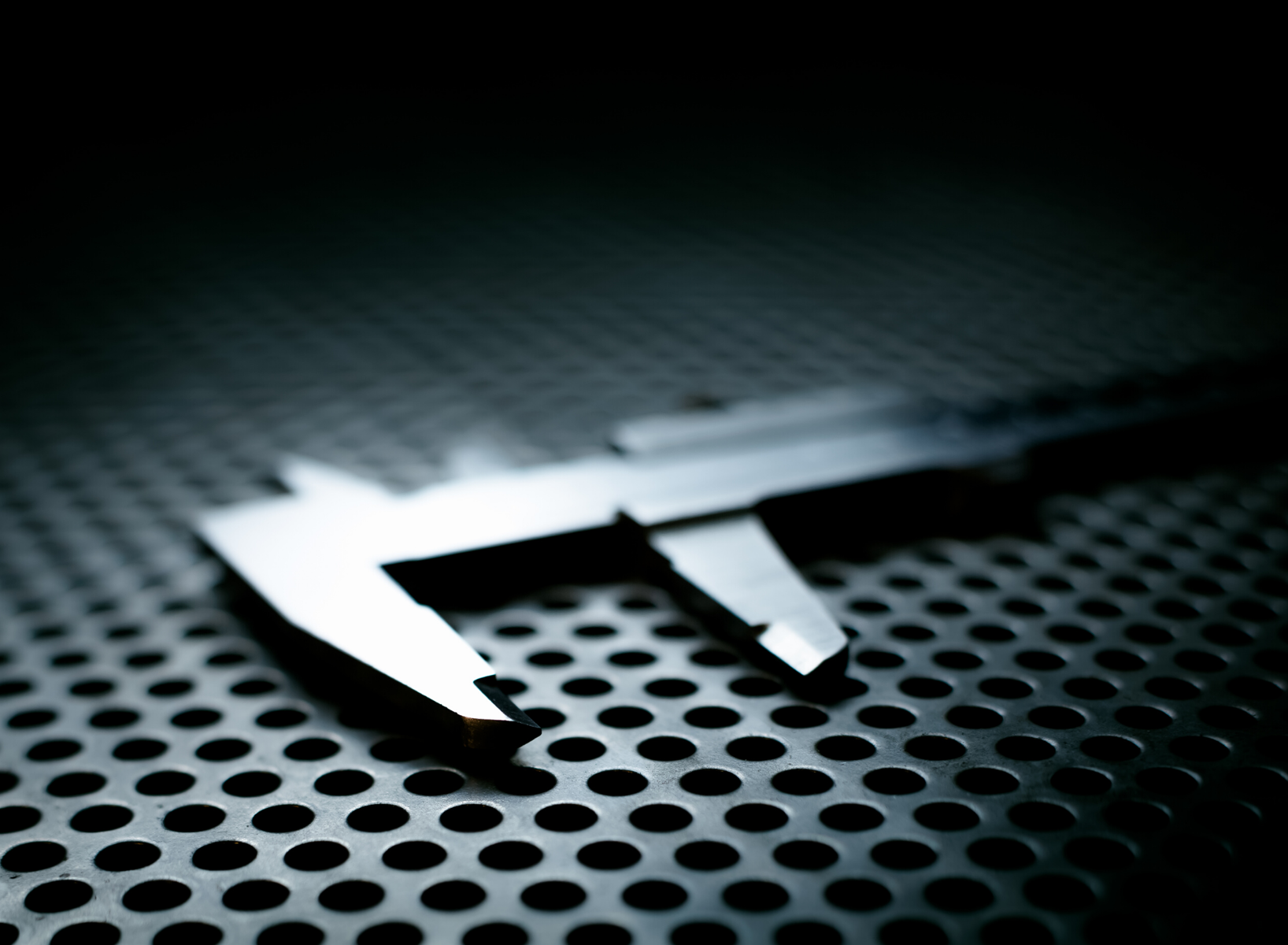
A few millimetres can cause huge problems: Why wear ring clearances matter
In this blog post we highlighted pump symptoms that could mean a clog is forming. If you are struggling with clogging, today’s post will explain why wear ring clearances should be one of the first things you check!
Wear ring clearances may be measured in millimetres, but they can cause a whole host of issues for your pump and system if not maintained in the recommended ranges. Of course wear rings should be replaced whenever they fall outside of the manufacturer’s recommendations, but an easy rule of thumb to remember is to replace wear rings when the original clearance has doubled. Read on to learn some of the big problems these tiny clearances can cause.
Pump efficiency: As fluid passes through the impeller, it is expelled through the casing volute channel. When wear ring clearance reaches a certain amount due to worn out wear rings, internal re-circulation results. This means internal pressure is flowing back to the low pressure side of the impeller, lowering the pump’s efficiency as well as its discharge pressure and flow. Basically the fluid is circulating around and around inside the pump instead of entering and exiting in an efficient and timely manner.
Vibration: This internal re-circulation can also cause excessive vibration if the wear ring clearances are too large. Eventually this will result in mechanical seal and bearing component damage.
Cavitation: Internal re-circulation also increases the NPSHR which can lead to cavitation damage to the impeller. Reducing this re-circulation by keeping clearances within recommended limits lowers the pump’s NPSHR and thus its cavitation as well.
Clogging: When a pump is installed in a wastewater application, foreign matter within the process fluid such as grit, rags and wipes is a given. Enlarged wear ring clearances allow this foreign matter to become tangled between the impeller suction hub and casing wear ring which can increase your clogging headaches.
Internal stresses: As radial wear rings also act as a bushing, enlarged wear ring clearances expose the pump to additional radial loadings. These additional radial loads cause stress to the bearings leading to premature pump failure.
Seal separation: These radial loads may also cause shaft deflection which results in separation of the mechanical seal faces during operation. This separation allows process fluid to enter and contaminate the seal chamber and eventually will make its way into the stator housing, which is the dry chamber of pump.
Power Consumption: Of course as pump efficiency decreases, its power consumption increases. The lost efficiency due to re-circulation will mean the pump may need to operate longer or at higher speeds to maintain the system demands. This additional energy consumption comes at a cost which will certainly add up over the course of a year.
Don’t let a few millimetres cause premature failure in your pumps. Protect your investment by making sure your pumps are getting the preventive maintenance they need. We’ve put together an easy Preventive Maintenance Checklist to help. Or, if you would rather leave maintenance to the pump experts, give us a call to schedule a site visit.