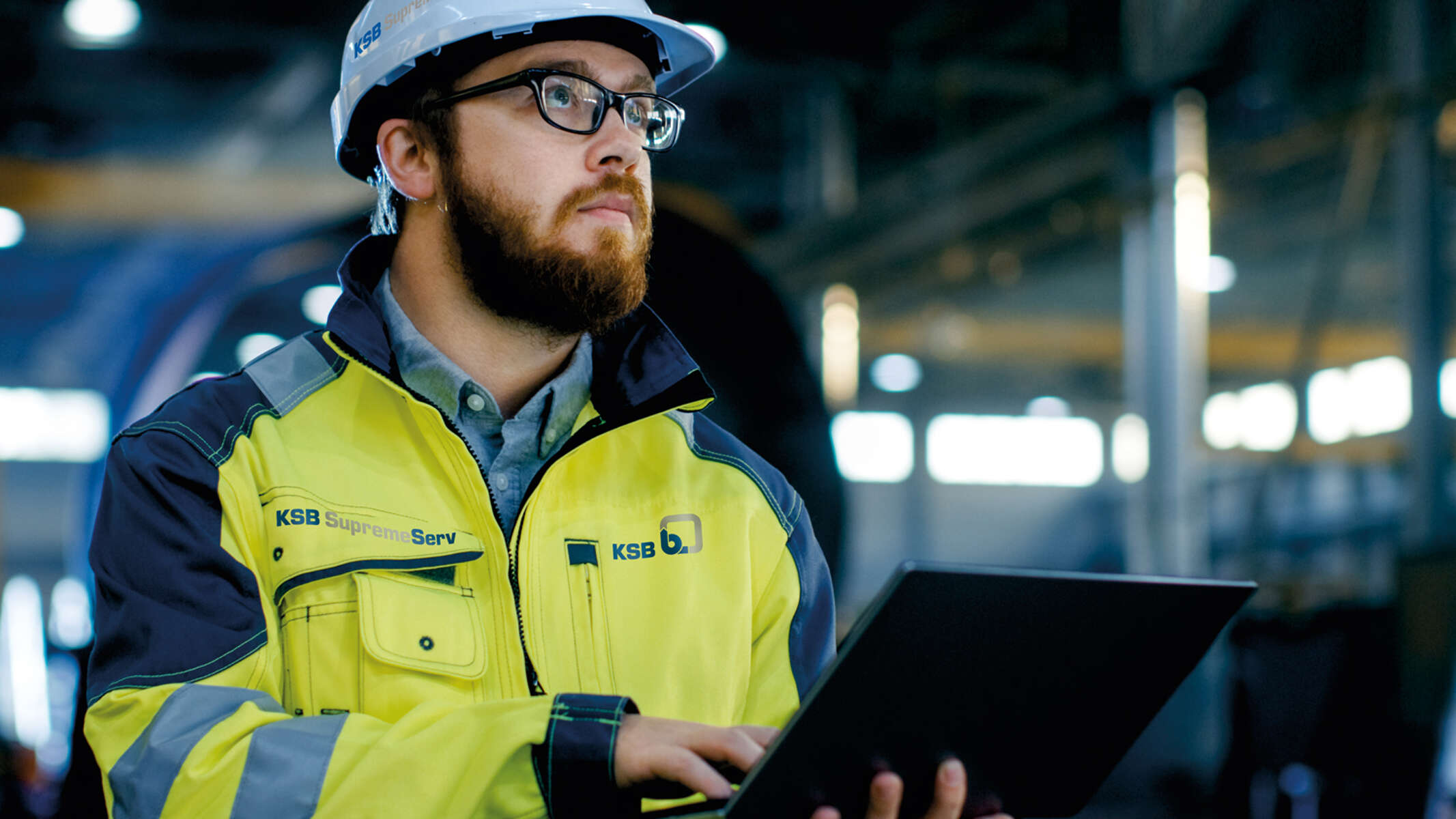
Maintenance 4.0: How digitalisation will simplify maintenance.
The fourth industrial revolution comes with many new digitalisation and automation opportunities many companies are already making use of. And with good reason.
The fourth industrial revolution comes with many new digitalisation and automation opportunities many companies are already making use of. And with good reason.
Why maintenance management is of major importance
Growing cost pressure forces many companies to look for new ways of increasing efficiency. At the same time, most of the potential for saving and rationalising has already been exploited. More and more companies are therefore identifying maintenance as a real factor for creating value. “Maintenance 4.0” is the buzzword in this context. Preventing unscheduled downtimes by detecting signs of wear and defects at an early stage bears the potential for enormous savings. This is where Industry 4.0 offers diverse opportunities that will radically re-shape maintenance in the future. Read on to find out more.
Systems are subject to continuous wear – and this not only affects moving components: Even when a system is only used rarely or not at all, its technical functionality can become significantly impaired. Components containing iron might start to rust, plastic or rubber seals might become porous, or the viscosity of oils used might decrease. Neglecting maintenance management can have considerable negative impacts on the quality level of production as well as on business processes overall.
In the worst-case scenario an undetected fault or damage can cause a complete system to fail and the entire production process to come to a standstill. The consequences of neglected maintenance are not to be underestimated either: The failure of a single component, for example a flaw in material, can cause major damage down the line. This is why maintenance is becoming a crucial success factor for many companies.
Maintenance management has increased in significance
The importance given to maintenance has grown over the last few years. One of the main reasons behind this development is the steady increase of global competitive pressure. This has led to the Overall Equipment Effectiveness (OEE) – a key indicator of a plant’s productivity – gaining in significance. Maximum availability and resource efficiency are key figures in this context.
Enhanced maintenance strategies primarily aim to extend the service life, shorten scheduled and prevent unscheduled downtimes – in other words: They aim to maximise the plant's availability.
The technical complexity of plants has increased rapidly over the last decades, with production systems now being tightly interlinked with each other and safety stock often avoided. A fault in a partial process can quickly cause entire process chains to fail, which entails major economic consequences. This has brought about a shift in perspective with maintenance moving closer towards production and resource planning and being perceived as a decisive success factor.
Using digital solutions can be particularly helpful: Based on the status data of machinery, impending damage can be detected in advance and maintenance measures implemented at an early stage. This is an opportunity for lowering maintenance costs and preventing the costs of downtimes as much as possible.
Especially in a world of increasingly complex production processes the topic “Maintenance 4.0” is gaining in significance.
Maintenance in the past and present
Just like the industrial history with its different generations (Industry 1.0 to Industry 4.0), maintenance, too, can be divided into generations. A general distinction can be made between the different maintenance strategies used:
- Maintenance 1.0, until approx. 1960: reactive maintenance; repair following a system failure; also referred to as “breakdown maintenance”.
- Maintenance 2.0, until approx. 1980: preventive, time-dependent maintenance. The focus shifted towards availability, service life and lower costs.
- Maintenance 3.0, until approx. 2015: condition-oriented maintenance by manual measures. Added to the aspects of Maintenance 2.0 were points such as consistent and/or higher product quality, increased plant and environmental safety as well as a higher profitability.
- Maintenance 4.0, from approx. 2015: condition-oriented maintenance by permanent digital monitoring, condition monitoring, etc.
Today, Maintenance 4.0 is a key component in the value creation chain of any smart factory. Maintenance ensures the stability, functionality and integrity of highly complex 4.0 systems. Sensors and cyber-physical systems as well as the IoT (Internet of Things) play central parts.
Smart sensors and digital twins
In the era of Maintenance 4.0 machinery has become “intelligent”:It indicates trends and automatically alerts the user of possible faults or component failures. This is realised by means of smart sensor technology, fitted on individual components or entire systems, that continuously collects data about the machine's condition (e.g. temperature, pressure, current input or vibration). Based on the data collected and all other known object information digital twins can be created: digital 1:1 images of the real object. These digital twins enable the implementation of complex analyses and simulations, forming the basis for Industry 4.0.
The collected data are documented as part of digital “system history files”. These comprehensive digital files are fed with data of all components fitted in the system. They especially serve to continuously document the life cycle of a system, providing valuable up-to-date knowledge that can be used for working on the system, making decisions, as evidence for completed tasks and as a basis for communication. Considering that such data frequently comes from different manufacturers universal interfaces are required to properly combine and consolidate the data available.
The data supplied by the digital history file not only helps to schedule maintenance more accurately but also to consolidate maintenance in different parts of the system, for example. Apart from the service jobs carried out, the file also shows all modifications to the system, which is of major importance in spare parts management. Digital monitoring devices can be set to automatically send a push message to the operator if a deviation from normal operation has occurred. These messages too will be stored in the history file, where they can be edited or accessed at any time. This allows the maintenance team to keep an eye on their system at all times and to know exactly when a failure might occur and maintenance is necessary. Based on this information the team is able to order spare parts in time and efficiently coordinate service jobs. Tasks can be performed in advance so that system downtime can be kept to a minimum.
In conclusion, predictive maintenance will become more and more relevant for production to be competitive. According to a current study* by the World Economic Forum and the Accenture consulting company 12 % of costs can be saved when carrying out scheduled rather than unscheduled repairs. Likewise, almost 30 % of maintenance costs can be saved using this approach. In addition, the share of unscheduled downtime can be reduced by up to 70 % according to the study. Another study* by Roland Berger shows that predictive maintenance only uses 15 % of the time for maintenance jobs compared to 40 % for “reactive” maintenance.
The main advantages of Maintenance 4.0 at a glance:
- Gaining a deeper process understanding through transparency in the system
- Enhancing profitability by reducing planned and preventing unscheduled downtimes
- Consolidating and planning maintenance based on permanent analysis of data recorded (predictive maintenance)
- Increasing the efficiency of machinery as potential for improvement is identified
Digital data allows the maintenance team to keep an eye on their system at all times, so they know if and when failures might occur.
Maintenance 4.0 at the example of pump monitoring
A variety of smart products and services are now available to increase the efficiency and reliability of a pump in a targeted manner. The principle of a smart pump set is simple: Sensors and control units connected to the pump adapt its operation decentrally, automatically and autonomously. One of KSB’s most successful smart factory solutions is KSB Guard, a comprehensive cloud solution for remote monitoring of pump populations and other rotating equipment.
KSB Guard, comprising a sensor and a cloud application, enables you to keep a mobile eye on the status data of your pump at all times. The functionality of KSB Guard is a simple as it is effective: A technical unit (sensor unit) fitted at the pump regularly monitors its temperature and vibration values and sends the recorded data to the gateway via a transmission and battery unit, linking it to the KSB Cloud. Measured data and additional information on the pump can be accessed conveniently and easily using the KSB Guard web portal or KSB Guard app.
Via the web portal or app operators are not only able to keep an eye on the load conditions as well as vibration and temperature values of their pumps, they can also set individual limits for each pump’s measured values. Should a change in system conditions occur, KSB Guard will inform the operators in due time, either per e-mail or per push message. With its integrated operating hours counter KSB Guard can tell when a bearing's life is about to expire. Also, system operators can always access the complete maintenance history of their pump via the app or web portal. This is where all sorts of details referring to a maintenance measure can be stored. By recognising trends operators can initiate maintenance work for a pump set at an early stage. This facilitates the planning of maintenance jobs, prevents unscheduled maintenance and increases the overall availability of pumps significantly. A practical aspect: KSB supports its customers with comprehensive services, such as spare parts service or reverse engineering.
Success story InfraServ Wiesbaden (ISW), Germany
ISW has been operating the 96-hectare Kalle-Albert industrial park since 1997. 24/7 ISW supplies the industrial park with about 22,000 cubic metres of compressed air per hour at a gauge pressure of 5 bar. To reliably and continuously keep an eye on the cooling water pumps of the compressed air system, ISW has chosen the KSB Guard monitoring unit. KSB Guard offers ISW production management and KSB technicians round-the-clock access to all pump status data via the web portal.
Just as well: A deviation from normal operation was reported on one of the pumps in October 2019. When KSB Guard detected excessive vibrations and output a relevant warning, InfraServ Wiesbaden was informed automatically and immediately. This helped ISW prevent impending bearing damage at an early stage and initiate repair in their own workshop at a time when pump operation was not essential. If one pump had suddenly failed, a second pump would have cut in to maintain the compressed air supply. Nevertheless, it was thanks to KSB Guard that a sudden system failure with unscheduled downtimes and very high repair costs was avoided.
In the Kalle-Albert industrial park in Wiesbaden KSB Guard detected high vibrations at one of the pumps. Technicians initiated a repair during periods when pump operation was not essential, preventing a sudden system failure with unplanned downtimes and far-reaching resultant losses.
Conclusion
How Maintenance 4.0 helps radically simplify maintenance
Using smart sensors and IoT technologies offers new opportunities to increase OEE – thanks to Maintenance 4.0. Because intelligent machinery practically lets you know when its operation deviates from the norm. Using these new technologies is especially recommended where large and expensive machinery is operated around the clock and where unpredicted downtimes may have serious consequences. However, given the low investment costs, digitalisation is also worthwhile for less complex systems.
Have you got any further questions? We look forward to hearing from you. Drawing on its comprehensive expertise in digitalising system components, KSB is happy to support you in making your company fit for Maintenance 4.0.
*https://digital.oup-fluidtechnik.de/o-p-fluidtechnik-4-2016/56531515/18
https://www.industry-of-things.de/amp/wartung-40-senkt-kosten-a-541428/
https://www.yumpu.com/de/document/read/62212195/industrieanzeiger-1118 (Seite 46/47)
Used products
KSB Guard
The smart and comprehensive monitoring service for pumps and other rotating machinery, available 24/7 and also for non-KSB pumps. Benefit from predictive maintenance with KSB: comprehensive transparency, increased availability, enhanced operating reliability and efficient operation (of fixed-speed pumps). Important operating data such as vibrations, temperature, operating hours and load condition (of fixed-speed pumps) can be accessed via KSB Guard, anytime and from anywhere. In addition, deviations from normal operation trigger immediate notifications via the KSB Guard web portal and/or app. The experts at the KSB Monitoring Centre also provide support in analysing causes.