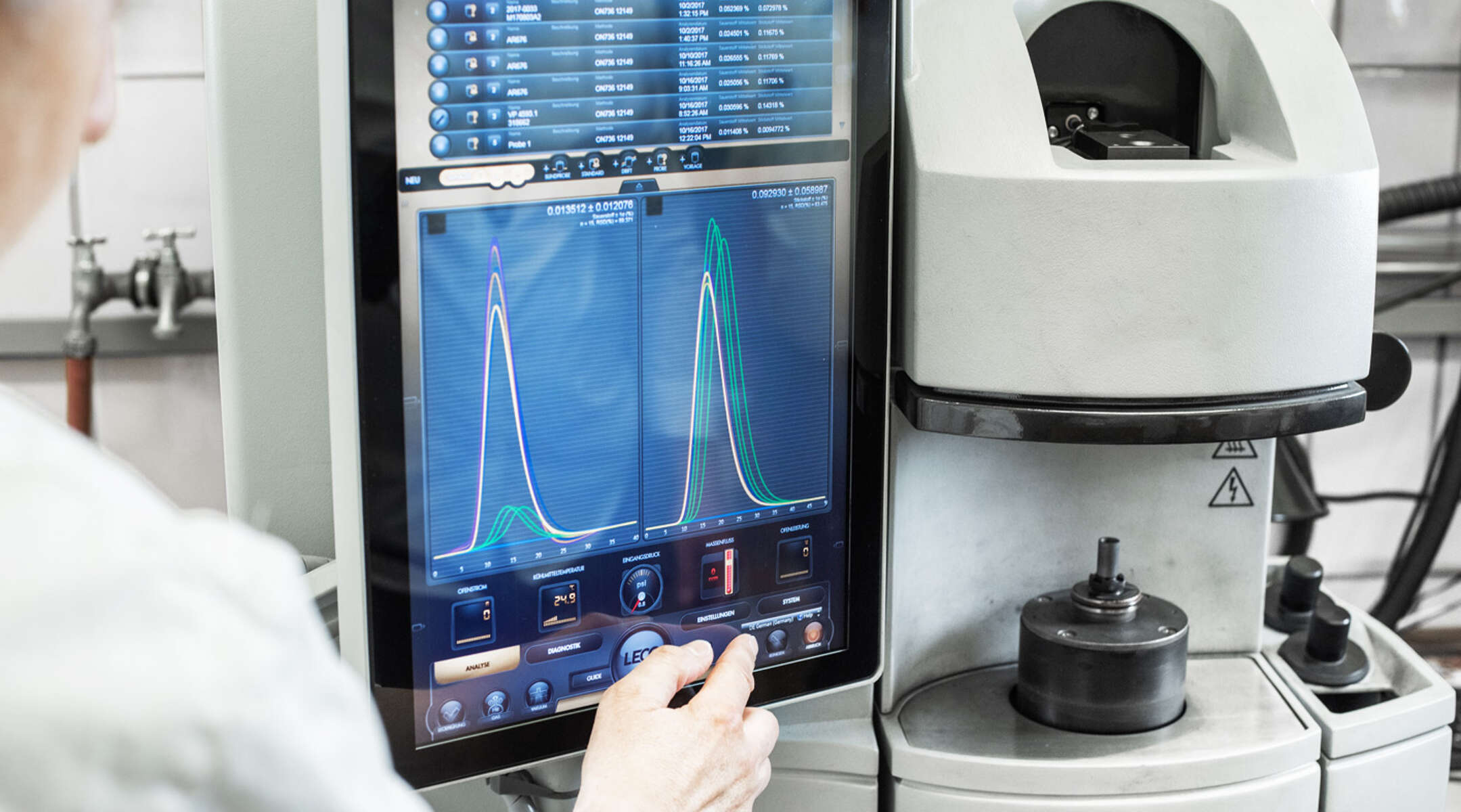
Trust is good, testing is better: a day in the KSB test laboratory
At our ISO/IEC 17025-accredited test laboratory for materials, KSB experts subject a vast range of materials and components to a wide variety of mechanical tests and chemical analyses to the highest international standards. How exactly does this operate? To find out, we accompany the materials experts for a typical day in their exciting work.
At our ISO/IEC 17025-accredited test laboratory for materials, KSB experts subject a vast range of materials and components to a wide variety of mechanical tests and chemical analyses to the highest international standards. How exactly does this operate? To find out, we accompany the materials experts for a typical day in their exciting work.
Morning: conference and correspondence
"I just love getting to the bottom of things!"explains one of the experts. He is an engineering graduate and trained materials tester who has been working at KSB for more than ten years – and for a few years now he and his colleagues have been carrying out extensive tests on materials and components here in KSB's own test laboratory in Pegnitz. "I find it really exciting to see what a component like this can withstand or how it reacts to certain influences," he continues. It is not only KSB's internal departments that benefit from the many years of experience and the state-of-the-art equipment, but increasingly it is also external customers and customers from outside the industry who regularly make use of the expertise of the laboratory for their own benefit.
The day at KSB's materials laboratory starts at around 8 am. We meet a colleague from Additive Manufacturing, the production department that is also based here at the Pegnitz site. The colleague reports enthusiastically about how they "printed" a complete pump casing with integrated heating channels from 316L stainless steel using selective laser melting, a 3D printing process – almost 60 % lighter than the cast original, but with the same degree of stability! Question: Can the test laboratory confirm this strength?
8:30 am: Video conference with an engineering contractor The company needs help because when they signed a contract with one of their customers, it was not clear that materials with special approval were needed for the installation of the system. KSB Sales Support had then turned to the test laboratory for help. In the online meeting, it turns out that the materials used by the engineering contractor do meet the customer's requirements. Just to be on the safe side, it is agreed that the casting batch from which the pump is cast will be specially examined again in the test laboratory.
Once the meeting is over, correspondence is the order of the day: an urgent enquiry from an operator of a large chemical plant is waiting in the inbox. Non-destructive materials testing is to be carried out on their premises. In practice, this means a comprehensive analysis using a transportable alloy analyser plus a mobile hardness test as well as microstructural replicas of the metal structure. No problem. This external assignment is promptly coordinated over the phone. Finally, a positive response to the request is sent to the operator by e-mail, together with a request for more precise arrangements to be made in the near future.
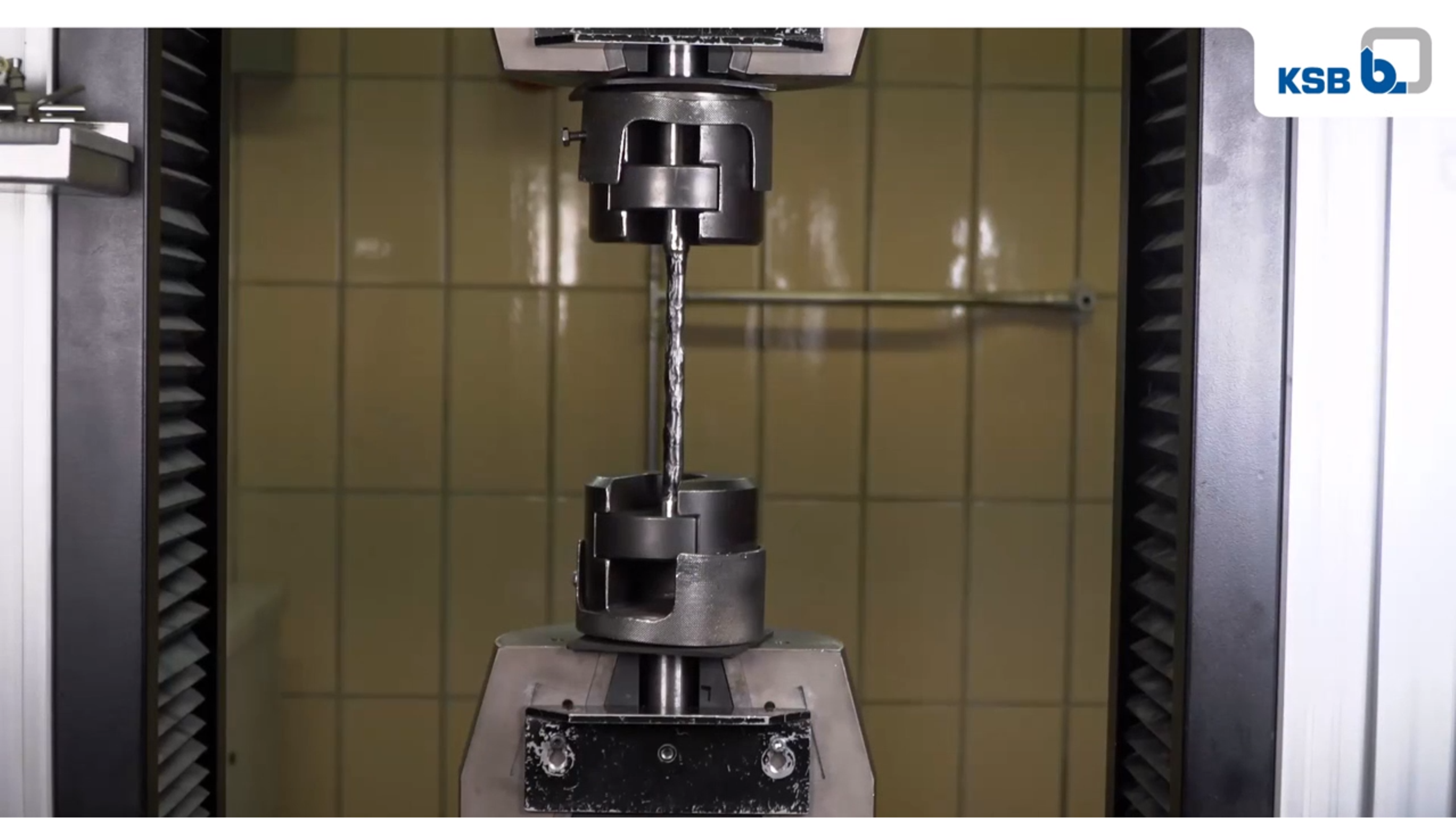
Morning: step-by-step tests for casting batches
10:00 am: Now the real fun at work begins - it's over to the test lab! First task: routine quality control of cast batches from the company's own foundry. The batches are successively subjected to a variety of tensile tests and notched bar impact bending tests. All tests are meticulously recorded so that a precise report can be compiled later. Today there are no complaints: as ever, the colleagues in the foundry have done their best work.
And straight on to the next job: two materials are to be tested for an internal customer who works in the field of valve production. The first is intended for an application in the power plant sector. This turns out to be quite demanding, as the material must withstand extreme temperatures. To perform the test, the oven of the tensile testing machine must first be brought up to temperature. Finally, the tensile test is carried out at 600 °C. The other material is intended for use in a chemical plant. Temperature also plays a role here – but in the other direction: in the notched bar impact bending test, the specimens are first cooled down to -40 °C in the cooling basin and then tested using an impact testing machine. Meanwhile, a colleague prepares a weld seam sample. A hardness test and a bend test are to be carried out.
A materials expert from KSB examines a metal powder material sample with a scanning electron microscope (SEM).
Lunchtime: a break and a chance to chat with colleagues
12:30 pm: Lunch in the canteen. Colleagues report on an interesting case of damage that they are currently working on. They have hardly got back to their desk when an external customer calls who has been very satisfied with the test laboratory in the past. He needs a tensile test and a material analysis at fairly short notice, to be carried out in an internationally accredited manner according to ISO/IEC 17025. No problem, it will be organised.
Afternoon: chemical analysis and meeting
1:30 pm: As luck would have it: just this morning, the colleague from Additive Manufacturing was reporting on his pump casing from the metal printer – and now these same additively manufactured samples are to be subjected to a thorough quality control. More precisely, the aim is to check whether the chemical composition complies with the standard specifications and KSB's own standards. For this purpose, the samples supplied are ground in the workshop and then measured in the test laboratory. The measurement is carried out by spark emission spectrometry and X-ray fluorescence analysis. The results show that the samples are exactly as expected. Perfect.
A team meeting of the "Quality Circle" is scheduled for 3:30 pm. Every week, all colleagues dealing with the topic of quality assurance meet in the large meeting room. Some attend virtually by video link from other locations. The quality management representative of the test laboratory has prepared some charts and reports on current topics such as new inspection and testing instructions or upcoming internal and external audits. Today the meeting only lasts half an hour and then it's back to the desk.
A KSB materials expert prepares a test using an ultrasonic transducer to investigate cavitation resistance.
Early evening: Administration
4:00 pm: This is, of course, also part of the job of a materials tester: the last couple of hours of the day are usually devoted to administration. Logs must be documented and test reports need to be written, archived and sent to the respective customers. And some of the e-mails that arrived during the day still need to be answered. The colleague shrugs his shoulders: "Oh well, as long as this doesn't become more important than the actual work in the lab, it doesn't bother me." And it doesn't look that way at KSB in Pegnitz. Quite the opposite in fact: customers' demands regarding the materials used are continually increasing. And with them also the demand for chemical analysis and metallographic as well as mechanical materials testing. So it certainly won't become boring in the future either.
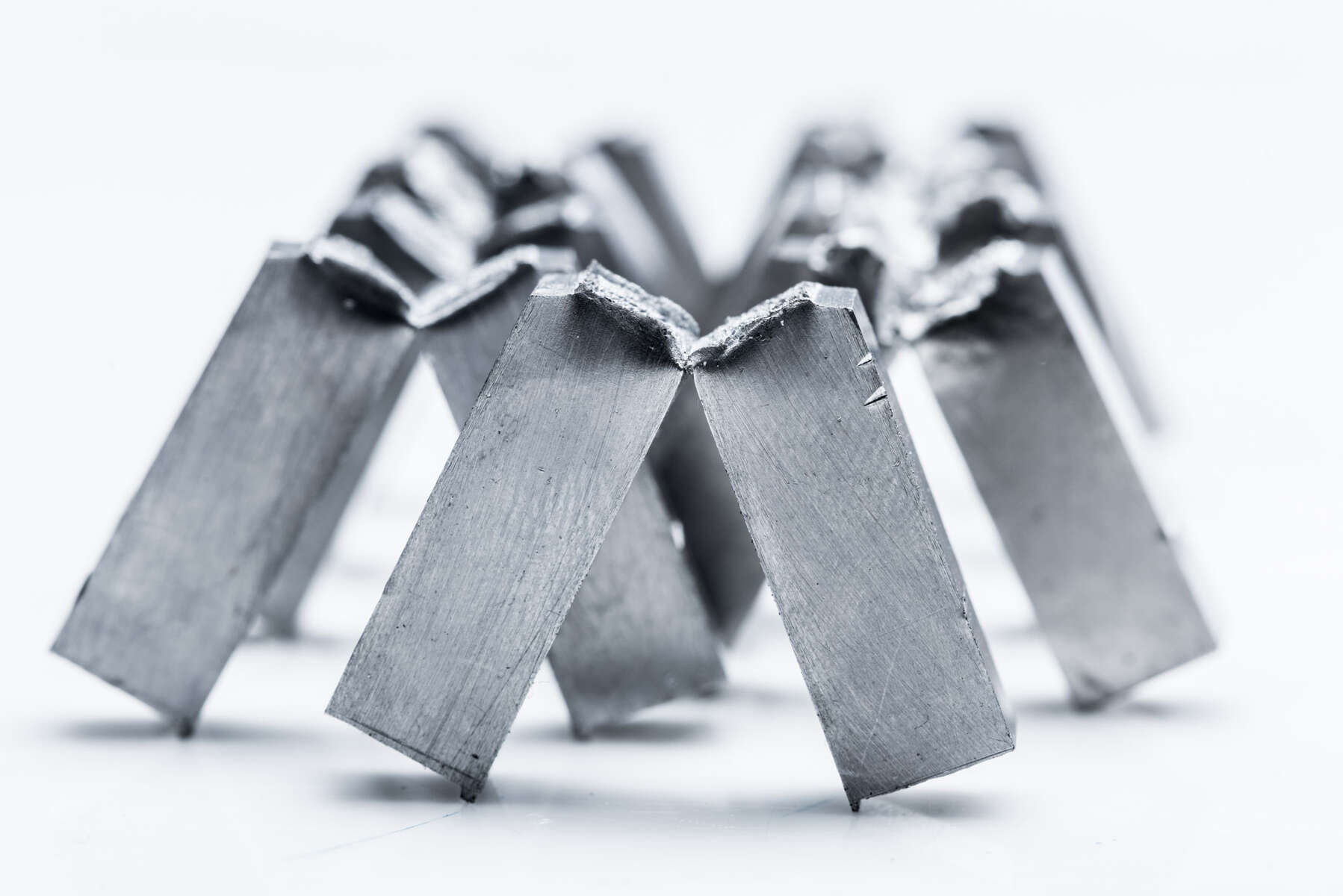
Materials expertise for durable products
To guarantee our customers reliable products, we have a dedicated competence centre for materials expertise. At our ISO/IEC 17025-accredited test laboratory for materials, we subject a vast range of materials and components to mechanical testing and chemical analyses to the highest international standards.
To guarantee our customers reliable products, we have a dedicated competence centre for materials expertise. At our ISO/IEC 17025-accredited test laboratory for materials, we subject a vast range of materials and components to mechanical testing and chemical analyses to the highest international standards.