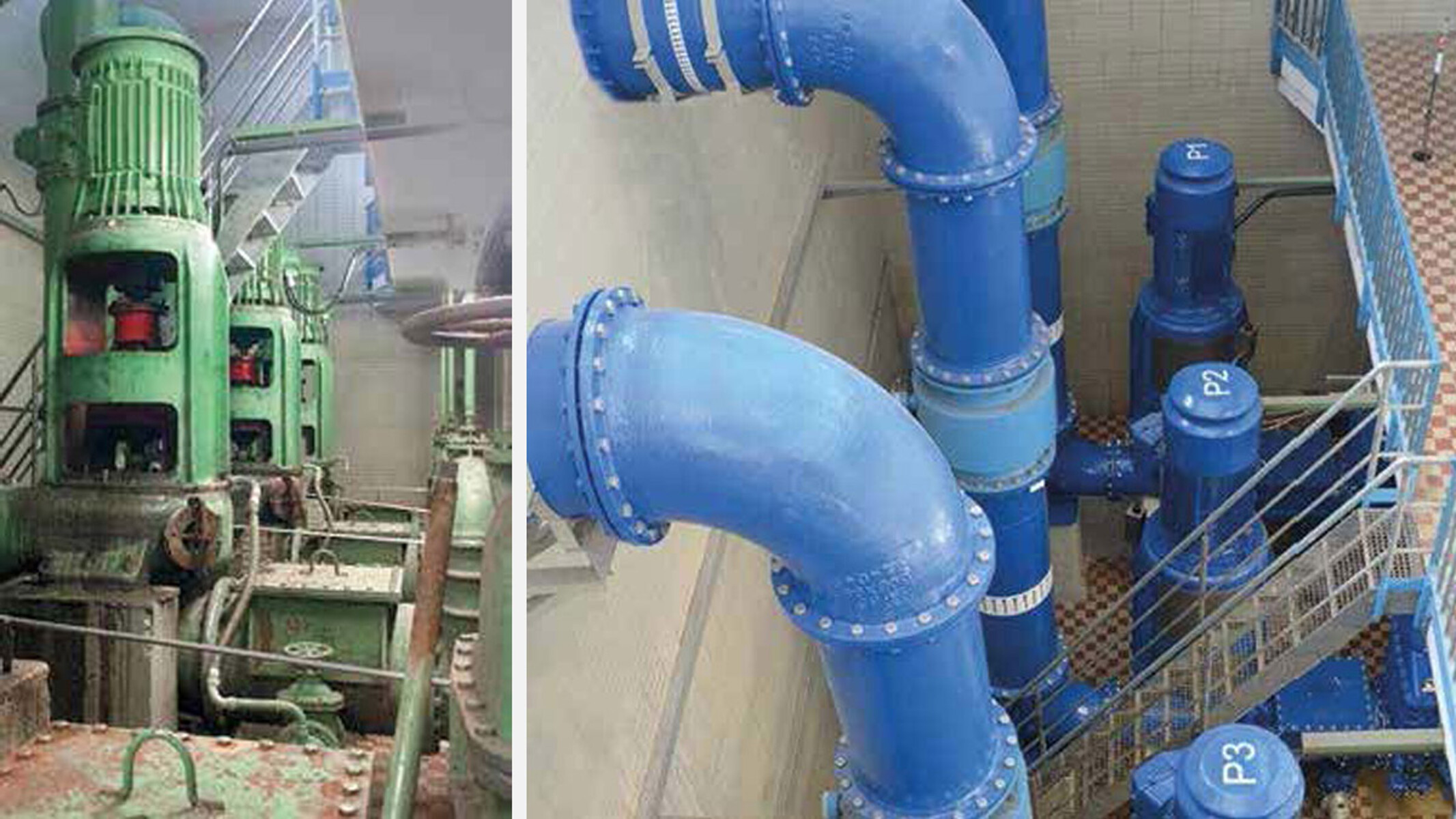
Equipped for the future: Refurbishing a waste water pumping station
Refurbishing an existing system often requires more know-how than setting up a new installation. The equipment being repaired may no longer be cutting edge, but it still serves its purpose for the operator. Comprehensive documentation may be missing and spare parts hard to come by. KSB SupremeServ specialises in these complex challenges and successfully applies a tailored catalogue of measures.
The project: Refurbishing the Hannover-Herrenhausen waste water treatment plant
The inlet pumping station of the Hannover-Herrenhausen waste water treatment plant has been working reliably for almost 60 years. It collects raw waste water from various city districts which is then transported to the different treatment stages. Refurbishment was necessary in order to secure the system’s operation for further decades.
Non-clogging impeller pump before and after cleaning
The customer: Stadtentwässerung Hannover
The utility company for the state capital of Lower Saxony has reliably disposed of the city’s waste water for over 115 years.
Collected from an area of approx. 450 square kilometres, Hannover’s waste water is pumped and transported via 2500 kilometres of public sewers.
Around 750,000 people benefit from the professional cleaning of waste water in one of the company’s two treatment plants.
The challenge: Repair and modernisation during ongoing plant operation
Although the refurbishment period was only scheduled to last 10 months, the plant had to remain fully operational throughout. This required close coordination between all parties involved. All work that had to be carried out on the system was announced and approved in good time.
Corrosion and wear had affected the pumping equipment and parts of the foundation. Alongside the modernisation and optimisation of the pump trains, the operator also requested a slight power adjustment to ensure that the pumping station is equipped for increasing waste water flow and possible heavy rainfall.
The solution: Customised measures – analysis, planning, organisation, maintenance, optimisation
KSB implemented the refurbishment project incl. risk analysis and repair work for Stadtentwässerung Hannover. The repair work covered not only the pumps, but also their drives, the requisite valves and the entire piping system.
Due to the pumping equipment’s age (approx. 60 years old), some of its technical documentation was incomplete and some spare parts were no longer available. KSB’s reverse engineering department was therefore commissioned to measure and reproduce five severely damaged three-channel impellers. The impellers’ diameters were increased to a maximum of 605 mm during this reproduction process. As the 16 gate valves installed could not be repaired, KSB supplied replacement valves; the swing check valve on the discharge side was refurbished.
After successful commissioning, KSB’s specialists provided instruction to the operating staff to ensure they became familiar with the new pumping equipment and the entire refurbished pumping station.
Pump and foundation before and after refurbishment
Figures I Data I Facts
Location: Hannover-Herrenhausen
Company: Stadtentwässerung Hannover
Over 2500 kilometres of public sewers serving 750,000 people over an area of approx. 450 square kilometres
Established: Approx. 1899
Sales revenue: Waste Water Technology
System: Hannover-Herrenhausen waste water pumping station
End user: Stadtentwässerung Hannover
Refurbishment work in detail
- Project planning, organisation and coordination – incl. risk analysis
- Provision of building site facilities incl. transport/lifting equipment and containers for offices, staff facilities, storage and washrooms
- Commissioning of the station including instructing the operating staff
- Complete documentation of the refurbishment work
- Disposal of all parts to be scrapped
- Pump service:
- Production of five three-channel impellers using reverse engineering
- Repair of four waste water pumps with three-channel impellers (KSB KWvd 350) – incl. conversion to double mechanical seals
- Refurbishing the pump foundations
- Test run on KSB’s test facility – incl. power and emissions measurement
- Motor service:
- Renewing and adapting the pumps’ drives
- Valve service:
- Replacing the four valves installed in each pump train (suction-side gate valve, gate valve for suction-side drainage, discharge-side knife gate valve and discharge-side flood gate)
- Supply of a new swing check valve for installation on the discharge side (protective grill)
- Piping service:
- Repair and coating of pipes
- Manufacture and installation of additional pipe supports
- Repair of sand traps
- Affixing signs incl. flow direction arrows
- Commissioning of the station including instructing the operating staff
- Complete documentation of the refurbishment work
- Disposal of all parts to be scrapped