Country, region and language selection
Europe
- Austria
- Belarus
- Belgium
- Croatia
- Czech Republic
- Denmark
- Estonia
- Finland
- France
- Germany
- Great Britain
- Hungary
- Italy
- Latvia
- Lithuania
- Netherlands
- Norway
- Poland
- Portugal
- Romania
- Russia
- Serbia
- Slovakia
- Slovenia
- Spain
- Sweden
- Switzerland
- Turkey
- Ukraine
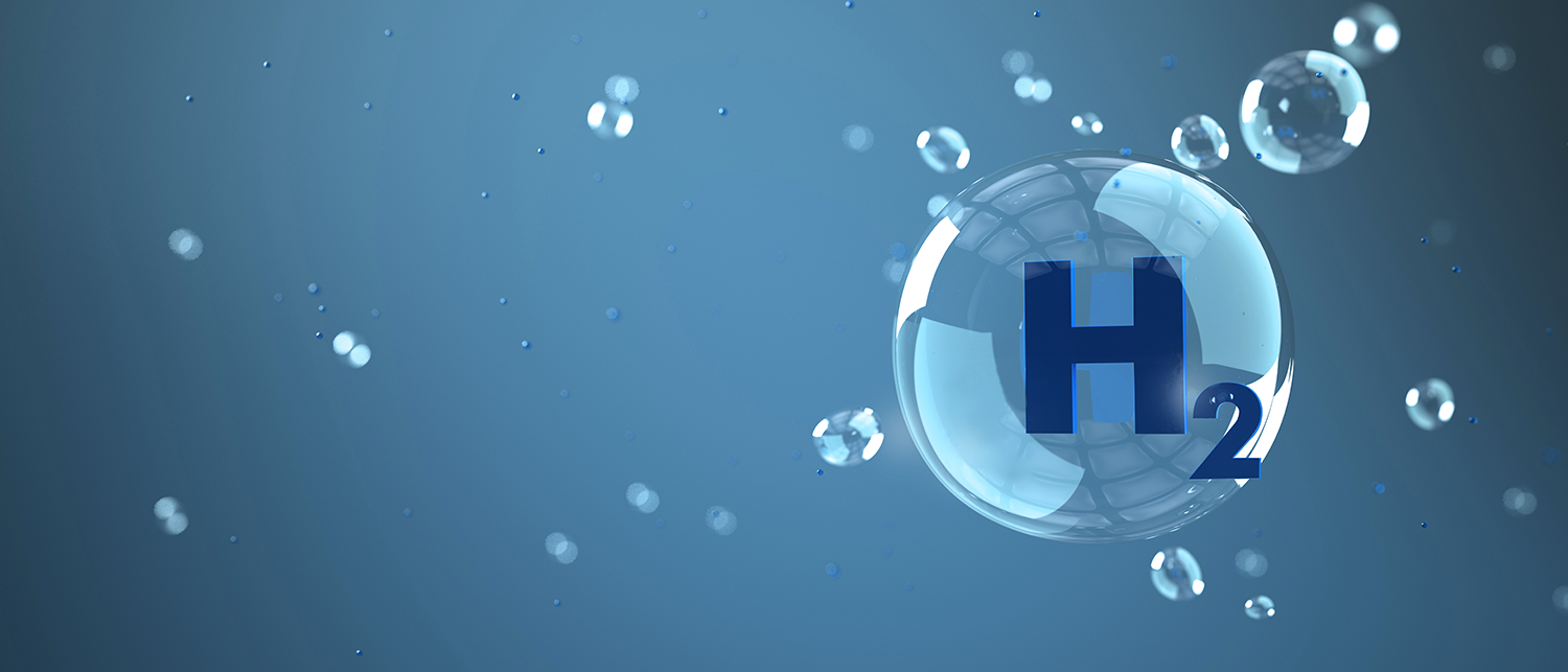
Pumps and valves for green hydrogen power
Along with the metal industry, the chemical industry consumes the most energy in Germany – and the majority of it still comes from fossil fuels. However, this will soon change when at least part of the supply will be replaced by green hydrogen. Discover why pumps and valves will play a decisive role in making this low-carbon switch.
Along with the metal industry, the chemical industry consumes the most energy in Germany – and the majority of it still comes from fossil fuels. However, this will soon change when at least part of the supply will be replaced by green hydrogen. Discover why pumps and valves will play a decisive role in making this low-carbon switch.
Decarbonisation drive in industry
Green hydrogen, i.e. hydrogen produced in a climate-neutral manner, is becoming increasingly important as an energy source for industry. Not only can this hydrogen be used to power vehicles and for storing renewable energy, it can also be used to defossilise material value chains. In refineries, for example, the “grey” hydrogen which is produced from the steam reforming of natural gas currently used to desulphurise the pre-products of petrol and diesel could gradually be replaced by its green counterpart.
In the steel industry, green hydrogen is already being used for the direct reduction of iron ore as an alternative to the furnace process with high greenhouse gas emissions, albeit so far only in pilot projects.
The prerequisite for such a switch is the development of an efficient and at the same time economical hydrogen economy – including the necessary infrastructure for the production, import, transport, storage and conversion of the gas. That’s the theory at least. In reality, many more details need to be considered when implementing such strategies.
Pumps and valves of today for the green industry of the future
As a technology company with engineering expertise in the fields of process engineering, petrochemicals and renewable energies, KSB has been active in the area of hydrogen technology for many years. Both its valve and pump portfolios already comprise many products that can be used in all stages of the hydrogen value chain. KSB can also draw on numerous reference projects and extensive experience gained with KSB products in known or piloted hydrogen production technologies, covering both blue and green hydrogen.
Materials experts are crucial for hydrogen applications
Hydrogen applications place high demands on the components used. Christof Lindner, responsible for hydrogen technology in KSB’s General Industry Market Area, explains the situation:
“A particular challenge when implementing hydrogen projects is that the detail requirements for the components used still vary greatly, for instance with regard to the materials.”
Consequentially, KSB not only commits its research and development expertise to customer projects but also contributes to relevant work groups set up by standardisation organisations (e.g. CEN in France and DIN in Germany).
KSB has the benefit of decades of experience in the chemical industry
As a supplier with decades of experience, KSB has the advantage of already being very familiar with the processes used in applications in the chemical industry. Especially regarding conversion processes (e.g. the production of ammonia) and grey hydrogen production processes based on fossil fuels (SMR, ATR, CCS), KSB is able to draw on its many years of experience. The same goes for valves that are used in chloroalkali electrolysis. Here, too, numerous companies have been relying on KSB’s diaphragm valves and butterfly valves for decades. Nevertheless, as Christof Lindner elaborates: “Many questions will ultimately only be resolved once development is more advanced and insights are available from a huge amount of operating hours.”
How can processes be scaled up for the hydrogen economy?
One of the biggest challenges on the path to a sustainable hydrogen economy is the size of future systems. At the moment, electrolysers are built on a modular basis using small subsystems. However, the question is whether modular container solutions or integrated large-scale systems/interconnected systems will prevail in future or perhaps even both?
This would obviously have a direct effect on the choice of pumps and valves used. While the flow rates with container solutions are around 10 m³/h, large-scale systems (according to studies) could easily reach 800 m³/h. Likewise, the operating pressure may range from 6 to 40 bar.
Larger modular systems may also have higher control requirements for optimum interaction of components. KSB offers both variable speed pumps and control valves for such applications. In large-scale integrated systems, the reliability of individual components could play an even greater role. Here, KSB already offers monitoring systems for supervision of operation and early detection of malfunctions.
Hydrogen electrolyser as a compact container solution: The flow rate here is around 10 m³/h.
As a supplier of pumps and valves, we not only need a broad range of products to cover a wide field of applications but also, in particular, a detailed knowledge of systems engineering, operating modes, materials and energy efficiency.
Christof Lindner, KSB
Ideal products and the necessary expertise for alkaline electrolysis
KSB’s products cover all of the main technologies in the green value chain, including various solutions for electrolysis – from alkaline electrolysis (AEL) and proton exchange membrane electrolysis (PEM) to promising future technologies such as anion exchange membrane electrolysis (AEM) and high-temperature electrolysis (HTEL).
Products employed to make the processes safer are seal-less pumps and diaphragm valves, such as the SISTO-16 or SISTO-20 type series, or butterfly valves, such as ISORIA or the KE type series, that are made of corrosion-resistant material or coated accordingly. Swing check valves from the SISTO-RSK or SISTO-RSKS type series with elastomer linings or ECTFE coatings, which require extremely short stabilisation distances and have no rotating components, further increase the reliability and continuous operation of the systems.
SISTO diaphragm valves only have two components that come into contact with the fluid handled: the valve body and the diaphragm itself. The diaphragm provides absolutely tight shut-off as well as hermetic sealing to atmosphere. SISTO’s unique sealing system features a diaphragm enclosed in the body and supported by a metal spiral in all valve positions. Depending on the application, diaphragm valves can be selected with optimally suited body materials, linings and coatings. Choosing the right diaphragm is key! In addition to elastomer diaphragms, KSB offers diaphragms made of TFM with an additional PVDF barrier foil as well as EPDM backing diaphragms.
Valves needed for cryogenic applications, such as the subsequent transport, are covered by the DANAÏS valve type series in the KSB portfolio. Furthermore, the fluidics specialists at KSB have accumulated experience with valves for liquid hydrogen (-253 °C) from optimising the Ariane rocket in test facilities.
Cutaway model of the SISTO-20 diaphragm valve from KSB. As you can clearly see, the stem and all internal operating elements are not in contact with the fluid.
Looking for the perfect pump? KSB has exactly what you need!
Magnochem volute casing pump with magnetic drive
Among the pumps tried and tested in alkaline electrolysis is the Magnochem horizontal volute casing pump with magnetic drive, available in close-coupled design or back pull-out design. “This seal-less pump has been used for many years whenever toxic, explosive or valuable fluids have to be pumped in industry. It is the ideal match for hydrogen technology,” Lindner explains.
With its magnetic drive, the standardised chemical pump is hermetically sealed, averting the risk of leakage. This plays a major role in alkaline electrolysis, where caustic potash is pumped that crystallises in contact with the atmosphere and can be harmful to health. Thanks to its close-coupled design, the pump set is ideal for tight installation spaces. Compliant with ISO 5199, the pump meets the toughest of quality standards and is available in a multitude of materials. With its broad range of hydraulic sizes and magnetic drives, Magnochem offers a large number of technically feasible variants, making it a good match for the most diverse of tasks in hydrogen production, and the user receives a pump with a maximum of safety, reliability and economic efficiency.
Movitec high-pressure centrifugal pump
Another pump suitable for hydrogen production is the Movitec multi-stage, vertical high-pressure centrifugal pump. "It is used for water treatment and pressure generation, for instance. It is designed for up to 40 bar and is very flexible with the number of stages and the option of speed control,” Lindner says about the pump’s application. Movitec’s compact design is a perfect match for installation in tight spaces, like in container solutions or modules. Even at low flow rates it can generate high pressures. With its comprehensive selection chart, it can be ideally matched to the different processes.
The Movitec high-pressure in-line pump is available in a wide range of variants – always perfectly suited to the specific application.
Next big thing? The further development of PEM electrolysis
Hydrogen technology involves more than just hydrogen production. Another key process is the sufficient supply of cooling water.
Pumps from the Etabloc/Etaline type series and valves from the ISORIA and SISTO-20 series are perfect for cooling heat exchangers. Thanks to their variable speed drive, the pumps impress with maximum energy efficiency. Their compact design makes them flexible and well-suited for installation in container solutions.
But of course there is not only alkaline electrolysis. PEM electrolysis is a much more recent technology that offers the benefits of a compact system design and high flexibility at changing loads. Compared to alkaline electrolysis, the process offers a lot of potential for future technical developments and cost savings. It also has the major advantage that it does not require the use of any risky chemicals.
The process is particularly interesting when looking at the aspect of hydrogen production from renewable energy sources becoming fit for mass production in the future. And the pumps? The toxic electrolyte aside, the conditions for use in PEM applications are similar to those in alkaline electrolysis. Already today, diaphragm valves and butterfly valves as well as various pumps made by KSB are used in pilot systems.
Fluidics experts are equipped for all eventualities
The pump and valve specialists at KSB feel well equipped for the tasks of future technologies, such as anion exchange membrane electrolysis (AEM) or high-temperature electrolysis (HTEL). The experts see a particular challenge in the high temperatures that place demanding requirements on materials. KSB is involved in several research projects to test new alloys for valves and their advantages when the components are exposed to such conditions.
Regardless which electrolysis process will be used in the future and what system size will prove more suitable, KSB’s portfolio covers the most diverse of requirements. And thanks to decades of experience, KSB offers pumps and valves that can be fine-tuned to the process to achieve the best efficiency as well as maximum safety and reliability.
Products used
Magnochem
Horizontal seal-less volute casing pump in back pull-out design, with magnetic drive, to DIN EN ISO 2858 / ISO 5199, with radial impeller, single-entry, single-stage. ATEX-compliant version available.
Movitec
Multistage vertical high-pressure centrifugal pump in ring-section design with suction and discharge nozzles of identical nominal diameters arranged opposite to each other (in-line design), close-coupled. With KSB SuPremE, a magnetless synchronous reluctance motor (exception: motor sizes 0.55 kW / 0.75 kW with 1500 rpm are designed with permanent magnets) of efficiency class IE4/IE5 to IEC TS 60034-30-2:2016, for operation on a KSB PumpDrive 2 or KSB PumpDrive 2 Eco variable speed system without rotor position sensors. Motor mounting points in accordance with EN 50347, envelope dimensions in accordance with DIN V 42673 (07-2011). ATEX-compliant version available.
SISTO-20
Weir-type diaphragm valve to DIN/EN with flanged ends, threaded socket ends or socket weld ends, in straight-way pattern; shut-off and sealing to atmosphere by supported and confined diaphragm; body with coating or lining, position indicator with integrated stem protection. All moving parts are separated from the fluid by the diaphragm. Maintenance-free.
ISORIA 10/16
Centred-disc butterfly valve with ISO 5211 compliant square shaft end, sealed by elastomer liner, with lever or manual gearbox, pneumatic, electric or hydraulic actuator. Wafer-type body (T1), semi-lug body (T2), full-lug body (T4) or U-section body with flat faces (T5). Body types T2 and T4 are suitable for downstream dismantling and dead-end service with counterflange. Connections to EN, ASME, JIS.